Синхронное производство и теория ограничений (Theory of Constraints, TOC)
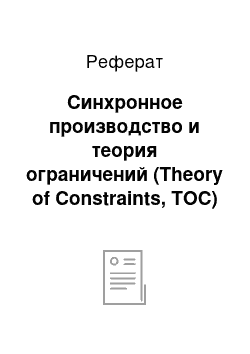
В MRP — системах используется обратное календарное планирование, от назначенной даты завершения производственного цикла, изначально ориентированное на составление графиков закупок материалов. Планирование загрузки производства — вторичная задача, причем в MRP — системах отсутствуют модули оптимизации загрузки, то есть балансирование мощностей и производственного потока возможно лишь методом проб… Читать ещё >
Синхронное производство и теория ограничений (Theory of Constraints, TOC) (реферат, курсовая, диплом, контрольная)
Теория ограничений разработана физиком Элиахом Голдраттом, которому довелось участвовать в создании системы управления производством на фабрике своего друга. Голдратт разработал оригинальную систему диспетчирования, благодаря которой объем производства на фабрике вырос втрое! Разработка была презентована в США под названием Optimized Production Tehnology (Оптимизированная технология производства). В 1986 г. Голдратт выпустил книгу «Цель: Процесс постоянного улучшения» (The Goal: A Process of Ongoing Improvement), изложив в ней основные положения своей концепции, названной позже Теорией ограничений.
Согласно Голдратту, ограничение — все то, что мешает организованной системе достичь своей цели. Любое предприятие рассматривается как система ресурсов, связанных между собой процессами, в которых они используются. Все ресурсы работают на достижение цели предприятия.
Можно выделить три типа ресурсов ;
- — недостаточный ресурс — «узкое место» — ресурс, мощность (или пропускная способность) которого меньше, чем потребность в нем.
- — избыточный ресурс — ресурс, мощность которого превышает потребность.
- — ресурс ограниченной мощности — ресурс, загрузка которого практически соответствует его мощности, но который, если работа не будет четко спланирована, становится недостаточным ресурсом.
Рассмотрим основные принципы производственного планирования по Голдрату.
Первый принцип: «не следует пытаться балансировать мощности, следует стремиться балансировать поток работ.
Действительно, классическая теория производства предполагает возможность достижения ритмичности за счет балансирования мощностей ресурсов, с тем, чтобы не было ни избыточных ресурсов, ни «узких мест». Но это редко возможно как минимум по четырем причинам:
- — не всегда существует ресурс (например, оборудование) требуемой по расчету мощности.
- — количество рабочих мест на отдельных операциях может быть только целочисленным, то есть расчетные значения приходится округлять либо в большую, либо в меньшую сторону.
- — балансирование мощности проводится на основе известных норм времени. Но фактическое время выполнения работы характеризуется определенным разбросом.
- — если необходимо гибкое производство, то говорить о единой норме времени вообще не приходится, поскольку для каждого вида выпускаемого продукта существует своя норма времени, а продуктовая структура и последовательность запуска партий определяется постоянно изменяющимися рыночными потребностями. Тогда балансирование мощности возможно только на основе усредненных величин с большим уровнем ошибки.
Таким образом, чтобы идеально сбалансировать мощности, все ресурсы должны быть избыточными, а следовательно, неэффективно используемыми.
Следующий принцип -«Основным объектом управления в теории ограничений являются ограниченные ресурсы, которым должен быть подчинен весь производственный процесс».
Определяется следующими соображениями:
- 1. Степень использования избыточных ресурсов определяется не их потенциалом, а другими ограничениями в системе.
- 2. Час, потерянный в «узком месте» — это час потерянный в системе в целом.
- 3. Час, сэкономленный на избыточном ресурсе — не что иное как мираж (поскольку такая экономия всего лишь увеличит на один час простой избыточного ресурса).
- 4. Производительность и уровень запасов определяется узкими местами.
Теория ограничений предлагает пять шагов управления системой:
- 1. Выявить ограничение системы («узкое место», критический ресурс);
- 2. Определить способы наиболее эффективного использования узкого места;
- 3. Подчинить весь процесс этому решению. Сделать все возможное для того, чтобы «узкое место» использовалось наиболее эффективно и оптимально
- 4. Повысить пропускную способность узкого места (т.е. устранить его, например, за счет привлечения дополнительных ресурсов);
- 5. Вернуться к шагу первому — т. е. не позволить инерции (старым методам управления, разработанным на втором и третьем шаге) превратиться в новое ограничение.
Как показывает практика, в компании, использующей ТОС, многие внутренние ограничения устраняются в период от одного до шести месяцев. При этом промышленным предприятиям благодаря оптимизации производственных заданий удается обойтись без дополнительных вложений в оборудование.
Каким же образом предлагается выявлять ограничения? Существуют два способа:
- — анализ шаблона мощности ресурса, в результате наблюдения за загрузкой каждого ресурса продукцией, прохождение которой через данный ресурс запланировано графиком. Уровень загрузки производственной мощности недостаточных ресурсов оказывается выше 100%.
- — Обобщение производственного опыта. При достаточном сроке работы системы «узкие места» хорошо известны производственным менеджерам, и их опрос совместно с наблюдением за производственной системой помогает выявить ограниченные ресурсы.
Если же анализ процесса невозможен, плановая загрузка не соответствует фактической, следует воспользоваться VAT — классификацией (см.ниже).
После выявления «узких мест» следует оптимизировать производственную систему.
Голдратт предлагает два направления оптимизации.
Первое — Создание механизма управления, привязанного к недостаточным ресурсам.
Поскольку пропускная способность всей системы определяется пропускной способностью недостаточного ресурса, следует максимизировать загрузку последнего, то есть недостаточный ресурс не должен простаивать.
Возникает вопрос — почему вообще возможен простой ограниченного ресурса, ведь его мощность по определению меньше потребности? Поскольку существует разброс времени выполнения каждой работы, особенно если поток работ неоднородный. Предположим, после работы, требующей меньшего время выполнения на этапах, предшествующих «узкому месту», следует работа с бОльшим временем. Тогда к моменту поступления на ресурс недостаточной мощности будет накоплен разрыв времени между двумя работами, который и обуславливает простОй недостаточного ресурса.
Для обеспечения постоянной загрузки недостаточного ресурса, следует перед ним создать резервные запасы — так называемый «амортизатор». Размер запасов может определяться на основании обработки статистической информации, с тем, чтобы допускать лишь минимальную вероятность простоя недостаточного ресурса.
С другой стороны, производственный поток перед недостаточным ресурсом не должен быть больше его пропускной способности, ведь тогда перед ним будут накапливаться запасы в незавершенном производстве.
Для этого следует установить контрольную точку на уровне недостаточного ресурса, ее называют «барабаном» (drum), который «выдает дробь» для управления всей системой. «Барабан» должен быть связан с ресурсом, определяющим уровень производственного потока, с тем чтобы выпускалось продукции не больше, чем выпускает недостаточный ресурс. Такая связь называется «веревкой». В случае линейной производственной системы это ресурс, задействованный на первом этапе производственного процесса.
Второе направление оптимизации — управление передаточными и обработочными партиями.
Партия обработки — это партия, которая обрабатывается на оборудовании без его переналадки. После завершения выпуска, производится переналадка оборудования на выпуск другой продукции (в случае серийной производственной системы). Поскольку переналадка предполагает единовременные затраты рабочего времени и материалов (вне зависимости от размера партии), исходя из экономической логики целесообразно увеличивать размеры обработочных партий. Но такое увеличение приводит к росту запасов в незавершенном производстве, увеличению общего срока производства, снижению гибкости производственной системы. Действительно актуальным является увеличение размеров обработочных партий только для недостаточных ресурсов, поскольку это увеличивает объем выпускаемой продукции. Но для избыточных ресурсов желательны меньшие размеры обработочных партий, поскольку в них лучше можно использовать время простоев.
Передаточные партии на практике часто принимаются равным обработочным, но это не обязательно должно быть так. Действительно, вместо ожидания выпуска полной партии, часть продукции, обработанная на предыдущей операции, может быть передана на последующую. Таким образом возможно сократить производственные запасы, общее время производства, сократить простои.
VAT — классификация.
В зависимости от характера производственных потоков, предприятия возможно разделить на 3 группы, каждая из которых характеризуется специфическими проблемами и путями их решения.
Квадратами на схемах изображены производственные операции.
Исходные ресурсы.
Предприятия типа V. | Предприятия А. | Предприятия Т. |
Процессы переработки сырья (Текстильная промышленность, нефтепереработка, химическое производство, производство бумаги, изготовление пластмасс). | Процессы сборки (Самолетостроение, автомобилестроение, машиностроение). | Процессы сборки из стадартных комплектующих (Бытовые приборы, предметы домашнего обихода…). |
Однородные технологические процессы, капиталоемкое специализированное оборудование, большая номенклатура. | Продолжительное время сборки, разнообразные технологические маршруты, неоднородность запасов, неоднородность потоков работ. | Наличие двух процессов: изготовления комплектующих и сборки. Сборочные процессы оперируют ограниченным количеством стандартных комплектующих. |
Проблемы — большие запасы готовой продукции, низкое качества обслуживания потребителей, недостаточная гибкость производства, непредсказуемое время производства, конфликты между подразделениями. | Проблемы — значительные запасы одних компонентов при нехватке других, существует как простои так и сверхурочные на одних и тех же операциях. | Проблемы — Большой разрыв между готовностью различных комплектующих, огромные размеры партий комплектующих и запасов, частое использование сверхурочных. |
Причины проблем — чрезмерные размеры партий, низкая загрузка, работа цехов оценивается по производственным критериям, увеличение производительности создает узкие места. | Причины проблем — большие размеры партий и отсутствие обратной связи. Не синхронизировано поступление на сборку различных комплектующих. | Причины проблем. Основное внимание уделяется управлению запасами, а не производственным процессом. Стремление к интенсификации мешает работе в соответствие с планами и прогнозами. |
Корректировочные мероприятия. Сокращение размера партий и времени производства, повышение качества обслуживания потребителей, сокращение запасов. | Корректировочные мероприятия. Использование системы «барабан-амортизатор-веревка», сокращение размеров партий. | Корректировочные мероприятия. Прекращение практики использования не по назначению комплектующих, сокращение партий комплектующих. |
В заключении следует отметить отличия синхронного производства, основанного на теории ограничений, от ранее рассмотренных систем JIT и MRP.
В MRP — системах используется обратное календарное планирование, от назначенной даты завершения производственного цикла, изначально ориентированное на составление графиков закупок материалов. Планирование загрузки производства — вторичная задача, причем в MRP — системах отсутствуют модули оптимизации загрузки, то есть балансирование мощностей и производственного потока возможно лишь методом проб и ошибок.
Системы JIT ориентированы на ограниченный ассортимент выпускаемой продукции, и относительно стабильный уровень производства, требуют наличия незавершенного производства, территориальной близости фирм-поставщиков. Таким образом, высокая эффективность JIT может быть реализована лишь при определенных условиях, не всегда имеющих место на практике.
В синхронном производстве используется прямое календарное планирование, сосредоточенное на критических ресурсах. Некритические ресурсы планируются позже, во вторую очередь, привязывая их к критическим ресурсам. Такая процедура обеспечивает выполнимость плана. Система синхронного производства может быть реализована в любой производственной системе.