Анализ обеспечения качества продукции на «ОЭМК»
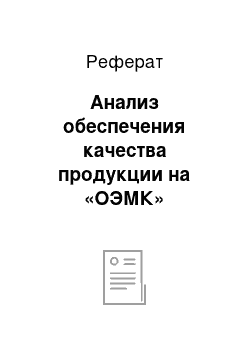
Проведенный анализ объемов производства и брака за 1994;1998 года показал, что в 1994;1995 годах все цехи металлургического цикла работали с превышением и на уровне их проектных мощностей. На 0,17% возрос брак в ЭСПЦ-2 и на 0,11% потери от брака по комбинату, что связано с усложнением сортамента стали. За 1996 год наблюдалось снижение объемов производства продукции, которое обусловлено… Читать ещё >
Анализ обеспечения качества продукции на «ОЭМК» (реферат, курсовая, диплом, контрольная)
Качество — это совокупность свойств и характеристик продукта, которые придают ему способность удовлетворять обусловленные или предполагаемые потребности. Качество — синтетический показатель, отражающий совокупное проявление многих факторов — от динамики и уровня развития национальной экономики до умения организовать и управлять процессом формирования качества в рамках любой хозяйственной единицы. Вместе с тем мировой опыт показывает, что именно в условиях открытой рыночной экономики, немыслимой без острой конкуренции, проявляются факторы, которые делают качество условием выживания товаропроизводителей, мерилом результативности и хозяйственной деятельности, экономического благополучия страны.
Качество продукции, включая новизну, технический уровень, отсутствие дефектов при исполнении, надежность в эксплуатации, является одним из важнейших средств конкурентной борьбы, завоевания и удержания позиций на рынке. Поэтому в современных условиях фирмы уделяют особое внимание обеспечению высокого качества продукции путем разработки и осуществления системы управления качеством продукции.
Система качества комбината разработана в соответствии с требованиями Международного стандарта ИСО 9002−87, введена в действие с 15 января 1995 года Приказом генерального директора и сертифицирована в марте 1995 года фирмой ТЮФ Берлин-Бранденбург сроком на 3 года (сертификат N 11 009 504 010) с проведением ежегодного надзорного аудита. Система обеспечения качества ОЭМК распространяется на производство металлизованных окатышей, непрерывнолитой заготовки, проката.
В связи с новой версией международного стандарта МС ИСО 9002−94 вся документация системы качества пересмотрена в 1995 году на соответствие требованиям нового стандарта, что было подтверждено в 1996 и 1997 гг. при проведении надзорного аудита фирмой ТЮФ Берлин-Бранденбург.
В апреле 1998 года действие сертификата на систему качества подтверждено фирмой ТЮФ Райнланд/Берлин-Бранденбург до апреля 2001 года. Регистрационный номер сертификата 09 100 85 036.
Оценка качества продукции основана на следующих концепциях:
- * качество продукции — отражает уровень качества самой продукции,
- * качество исполнения — отражает ту степень, в которой товары фактически удовлетворяют нужды клиентов;
- * качество соответствия — отражает ту степень, с которой продукция или услуги, предоставляемые фирмой, соответствуют внутренним спецификациям.
Обеспечение качества предусматривает разработку стандартов качества, распределение ответственности за качество и контроль качества работ. На ОЭМК Политика в области качества утверждена 15 января 1995 года и в течение 1995;1998 годов оставалась без изменения. С целью устранения несоответствия, выявленного фирмой ТЮФ Берлин-Бранденбург, и повышения знания Политики средним звеном было выпущено директивное письмо, предусматривающее повторное ознакомление персонала всех уровней в подразделениях комбината. Проведенная работа была подтверждена отчетами начальников подразделений. Знание политики в области качества персоналом проверялось при внутренних проверках и проверках технологии /35/.
С целью реализации, утверждённой политики качества в 1996 году в организационной структуре коммерческой службы были произведены следующие организационные изменения:
- — управление сбыта (УС) и отдел планирования договоров и балансов ОПДиБ) были преобразованы в управление планирования, договоров и балансов (УПДиБ);
- — организована новая служба — управления маркетингом (УМ). В связи с введением новой должности заместителя технического директора в организационную структуру технического управления были внесены изменения, касающиеся перераспределения полномочий между заместителем технического директора и заместителем начальника технического управления по технологии.
Руководство по качеству ОАО ОЭМК является документом первого уровня и содержит основные положения системы обеспечения качества на комбинате и ссылки на руководящие документы. Руководство документально закрепляет организационную структуру, распределение полномочий и ответственности между руководящими работниками акционерного общества, отдельными структурными подразделениями на всех этапах производства продукции, определяет границы их взаимодействия и является обязательным для исполнения, как всем руководством, так и всеми работниками акционерного общества.
Программа по качеству за 1998 год была выполнена за исключением обучения аудиторов внутренних проверок и преподавателей по системе качества, которые перенесены на 1999 год.
Согласно существующей на комбинате программе качества, ежегодно на комбинате проводиться анализ контрактов. Он осуществляется в соответствии с СТП СК 187 895−6.3−1-95.
В результате внедрения технических, технологических, организационных и контрольных мероприятий по повышению качества продукции в 1995;1998 годах стало возможным производство металла более сложного сортамента и для более ответственного назначения и использования в машиностроении. Данные по количеству производимых марок, новых марок, в том числе на экспорт приведены в таблице2.7., которая показывает, что количество выплавляемых марок возросло в 1998 году по сравнению с 1994 годом в 4,5 раза, в том числе новых — в 1,3 раза, в том числе на экспорт — в 4,2 раза, новых на экспорт — в 1,6 раза, доля экспорта в товарной продукции возросла на 4%.
Таблица 2.7 Производство новых марок стали, штук.
Период. | Выплавлено марок. | Выплавлено на экспорт. | ||
всего. | новых. | всего. | новых. | |
Благодаря усложнению сортамента и сертификации системы качества рынок металлопродукции ОЭМК в 1995;1998 гг. по сравнению с 1994 годом по числу контрактов фирм, стран, возрос в 1,5 раза. За 1998 год поступило 495 предложений на поставку продукции на экспорт, из них по 330 заключены контракты, что на 26% больше чем в 1997 году. В 1997 году по экспорту поступили предложения на поставку металла из 315 марок стали и по 230 маркам заключены контракты, остальные предложения были отклонены по причинам несоответствия:
- — химического состава (высокое содержание Cr, Ni, Mo);
- — размеров (прокат и НЛЗ вне пределов, возможных для ОЭМК);
- — конечного назначения металла — ШХ15 для производства шариков, штамповка без предварительного переката, детали большого размера без термообработки у потребителя. Данные по количеству фирм и стран, покупающих металлопродукцию комбината, и заключенным контрактам приведены в таблице 2.8.
Таблица 2.8 Количество стран, покупающих продукцию ОЭМК, штук.
Наименование показателя. | Период. | Рост, снижение. | ||||
Страны. | Н.д. | |||||
Контракты. |
Из общего числа контрактов выполнено в срок 94%. Невыполнение в срок 20 контрактов обусловлено несвоевременным производством продукции в связи с задержкой поставки ферросплавов и специальных материалов, необходимых для производства металла. Средняя цена металлизованных окатышей снизилась на 17.03 $, литой заготовки — на 32.44 $, проката — 3.45 $, что было обусловлено экономическим кризисом России и необходимостью резкого увеличения оборотных средств предприятия.
Контроль качества исходного сырья В целях обеспечения высокого качества продукции на ОЭМК устанавливают контроль на всех стадиях производственного процесса, начиная с контроля качества используемых сырья и материалов и кончая определением соответствия выпущенного продукта техническим характеристикам и параметрам. Поэтому контроль качества продукции на комбинате стал составной частью производственного процесса.
Входной контроль сырья и материалов осуществляет участок внешней приемки технического управления и цехи, в соответствии с требованиями СТП СК 187 895−6.10−95 /36/.
Перечень сырья и материалов, контролируемые параметры, вид и периодичность контроля, распределение обязанностей установлены в схеме входного контроля. Оценку сырья и материалов, не входящих в схему, производят по данным сертификатов специалисты соответствующих служб в соответствии со стандартом.
В 1995 году — в первый год внедрения системы обеспечения качества на комбинате входной контроль стал проводиться более тщательно в сравнении с предыдущим периодом. Возрос объем забракованных партий по огнеупорам и фритте. Имели случаи поставки сырья и материалов более низкого качества, чем это предусмотрено требованиями технологических инструкций. Например, влажное сырье и добавочные материалы, некачественные огнеупоры.
В 1996 году был введен дополнительно входной контроль медных плит для кристаллизаторов. Уменьшился объем забракованных партий по огнеупорным материалам на 0,54%.
Сырье и материалы, поступающие на комбинат без сертификата качества (34%), не выдавались в производства до их получения.
Имели место 10 случаев разрешения выдачи в производство материалов, не полностью отвечающих требованиям технологии.
За 1997 год увеличился объем входного контроля в 1,4 раза, объем забракованной продукции снизился на 0,2% по сравнению с 1996 годом.
Сырье и материалы, поступающие на комбинат без сертификатов качества и забракованные на входном контроле, в производство не выдавались. По специальному разрешению, как и в 1996 году имели место 10 случаев выдачи в производство такого сырья и материалов.
При внутренней проверке было выявлено, что не весь забракованный материал содержится в изоляторе брака.
За 1998 год при входном контроле установлено, что качество основного сырья и материалов соответствовало установленным требованиям, кроме ферросплавов и огнеупоров. По сравнению с 1997 годом было забраковано на 1% меньше партий ферросплавов и на 0.1% больше огнеупоров.
Данные входного контроля сырья и материалов приведены в таблице 2.9.
Таблица 2.9 Данные входного контроля сырья и материалов, кол-во партий, %.
Наименование сырья и материалов. | Изм. +/; | |||||
Проконтролировано, всего, в том числе: | ||||||
— огнеупорные материалы. | ||||||
— ферросплавы. | ||||||
Забраковано, всего в т. ч. | 14/3,33. | 19/3,17. | 20/2,6. | 17/2,5. | 14/1,1. | 0/2,3. |
— огнеупорные материалы. | 25/0,3. | 20/1,4. | 20/2,8. | 17/2,5. | 11/0,5. | |
— ферросплавы. | ; | ; | ; | 9/2,4. | 5/2,0. | 4/0,4. |
Процент партий с сертифик. | ; | 73,7. | ||||
Выдано в производство. | ; | ; | 10/1,3. | 10/0,9. | 11/0,5. |
Важным моментом при закупке материалов является выбор поставщика. На комбинате эти функции выполняются Техническим управлением и УМТО. Проведённая этими подразделениями в 1996 г. актуализация Перечня поставщиков с учетом их оценки дала следующие результаты:
- 1. Оценку поставщиков проводили по следующим критериям:
- — оценка системы качества путем анкетирования или аудита;
- — оценка по результатам входного контроля;
- — оценка результатов применения материалов.
- 2. В результате внутренней проверки за 1996 год установлено, что требования стандартов в основном выполняются.
- 3. Выявлены следующие нарушения:
- — заявки от цехов годовой потребности сырья и материалов УМТО принимает без обосновывающих расчетов;
- — цехи не представляют на конец месяца отчет о расходе и остатках сырья и материалов.
- 4. Выявленные нарушения устранены с внедрением системы АСУ (R/3) в IV квартале 1997 года.
- 5. В течение 1996 года из-за несоответствия отечественных огнеупоров условиям эксплуатации сталеразливочных ковшей с АКОС отказались от поставки их Запорожским, Семилукским огнеупорными заводами, а перешли на закупку у инофирм «Радокс» (Австрия), «Дидиер» (Германия), «Магнохром» (Югославия), «Керамика» (Словакия).
- 6. За 1997 год имели место отклонения от графиков по поставке лома и алюминиевой проволоки. В ряде случаев качество сырья и материалов не соответствовало требованиям договоров.
- 7. При внутренних проверках за 1998 год выявлены следующие несоответствия:
- — не все поступающие материалы проходили входной контроль;
- — копровым цехом, ЦОИ и ЭСПЦ не предоставлялись в ЖДЦ копии распоряжений о назначении ответственных за выгрузку вагонов;
- — в стандарты данного элемента не были внесены изменения в соответствии с приказом генерального директора «Об усилении ответственности при использовании товарно-материальных ценностей».
Все несоответствия устранены.
- 8. На основании оценки результатов применения огнеупоров за 1998 год установлено, что используемые для футеровки рабочего слоя стальковшей огнеупоры фирмы «Магнохром» не отвечают необходимым требованиям, а стаканы фирм «Файч-Радекс-Дидиер» превосходят по своим свойствам отечественные производства ОАО «Боровичский огнеупорный завод» (заключение огнеупорной лаборатории). Фирма «Магнохром» и ОАО «Боровичский ОЗ» (для погружаемых стаканов) исключены из Перечня поставщиков. Вместо ОАО «Боровичский ОЗ» в Перечень включена фирма «Файч-Радекс-Дидиер».
- 9. Исключен из перечня ряд поставщиков из-за отсутствия поставки в прошлом году (Днепропетровский метзавод — ферромарганец, Запорожский завод — силикомарганец, Стахановский завод — ферросилиций, СП «Комсак» — металлолом.).
- 10. На основании акта промышленных испытаний в Перечень включен поставщик бентонитовой глины — Иждеванское р/у.
- 11. Документацию на закупки (договора и контракты) оформляли в соответствии с требованиями стандарта. В связи со сложностью приобретения централизованным способом нормативной документации на закупаемые материалы и оборудование в стандарт внесено изменение, устанавливающее требование по согласованию договоров и контрактов с техническим управлением и в случае отсутствия НД на комбинате предусматривать в договорах и контрактах дополнительное условие по ее обеспечению.
- 12. По ряду позиций (металлолом, ферросплавы, огнеупоры) была задержка с поставками, что объясняется финансовым положением акционерного общества.
Контроль готовой продукции и технологии её производства Контроль готовой продукции и технологии её производства занимает одну из основных ниш в системе управления качеством.
С целью получения доказательств соответствия готовой продукции требованиям договоров и контрактов на ОЭМК проводятся все виды сдаточного контроля.
Контрольные лаборатории (химическая, физическая, механических испытаний) постоянно подлежат аттестации. Достоверность контроля химического состава подтверждается участием в межлабораторных испытаниях по аттестации стандартных государственных образцов.
Организация и проведение испытаний определены в стандартах предприятия. В связи с переработкой технологической документации в производственных цехах в 1998 году пересмотрен стандарт на организацию и проведение химического анализа. В стандарт предприятия на проведение механических испытаний внесено изменение, предусматривающее порядок контроля новых видов продукции и утвержден регламент проведения испытаний.
Результаты испытаний исполнители регистрируют в журналы, (распечатки ЭВМ), передают на участки ТК через систему АСУ. За 1998 год объем механических испытаний увеличен на 18.2% за счет изменения сортамента.
Готовую продукцию отгружают только с сертификатом качества, в которые заносят результаты испытаний.
Дубликаты проб и результаты испытаний хранят в соответствии с требованиями элемента СК 16.
Проведенный анализ объемов производства и брака за 1994;1998 года показал, что в 1994;1995 годах все цехи металлургического цикла работали с превышением и на уровне их проектных мощностей. На 0,17% возрос брак в ЭСПЦ-2 и на 0,11% потери от брака по комбинату, что связано с усложнением сортамента стали. За 1996 год наблюдалось снижение объемов производства продукции, которое обусловлено уменьшением заказов. За этот период удалось сократить процент брака в ЭСПЦ на 0,07%, в СПЦ — на 0,01%, но общие потери по комбинату остались на прежнем уровне. За 1997 год удалось достичь дальнейшего сокращения брака металлопродукции: в ЭСПЦ на 0,1% и в СПЦ на 0,02%, потери от брака уменьшились на 0,11%. Брак был вызван нарушениями технологии, плохой подготовкой оборудования, неритмичной работой цехов и неудовлетворительным обеспечением производства. Потери от забракованной продукции по комбинату от себестоимости продукции в 1998 году удалось уменьшить на 0.14% и составили 0.45% (12 378 тыс. руб). Сведения о браке продукции приведены в таблице 2.10.
Таблица 2.10 Сведения о браке продукции.
Вид продукции. | ||||
тонн. | %. | тонн. | %. | |
Литая заготовка, в т. ч.: | 13 525,95. | 0,93. | 13 046,70. | 0,83. |
Аварийный. | 2408,70. | 0,17. | 2245,40. | 0,13. |
В заготовке. | 3705,47. | 0,25. | 3438,53. | 0,17. |
В переделе. | 7338,95. | 0,50. | 7162,77. | 0,43. |
Сортовой прокат, в т. ч.: | 1182,15. | 0,09. | 915,59. | 0,06. |
При прокатке. | 567,60. | 0,04. | 593,62. | 0,04. |
При отделке. | 604,89. | 0,046. | 290,27. | 0,02. |
При обдирке. | 9,66. | 0,0007. | 31,7. | 0,002. |
Потери. | 0,72. | 0,61. |
Переведены в пониженные марки 1723 т стали в 1998 г., 4179 т. (из-за несоответствия химсостава — 62,5%) в 1997 г.; 1063 т. проката (1998 г), 1792 т., (из-за отсутствие заказа — 51,5%) (1997 г). Объемы производства продукции и полученного брака приведены в таблице 2.11.
Таблица 2.11 Объемы производства продукции и брака.
Вид продукции. | Период. | |||||
Откл. | ||||||
Производство, тыс.т. | ||||||
Окисленные окатыши. | 2410,8. | 2500,3. | ||||
МОК. | 1730,3. | 1890,2. | ||||
Сталь. | 1654,8. | 1720,5. | ||||
Прокат. | 1438,8. | 1520,4. | ||||
Брак металла ЭСПЦ-2,%. | 1,03. | 1,0. | 0,93. | 0,93. | 0,83. | 0,3. |
Брак СПЦ,%. | 0,11. | 0,09. | 0,08. | 0,08. | 0,08. | 0,03. |
Потери от брака по комбинату к себестоимости продукции, млн.руб. | 0,69. | 0,64. | 0,63. | 0,59. | 0,45. | 0,24. |
; | ; | ; | 16 470,9. | 15 909,3. |
Рекламации:
Данные по полученным рекламациям и дополнительным затрат по ним приведены в таблице 2.12.
Таблица 2.12 Рекламации.
Наименование показателя. | Уменьш. | ||||
Количество рекламаций, шт. | |||||
Заменено металла, тонн. | 56,4. | 126,3. | 51,6. | 279,4. |
В 1997 году из 126,3 т. замененной продукции по рекламациям 120,6 т. (95,5%) не удовлетворяло по макроструктуре, 4,5% - по поверхностным дефектам и длине.
За анализируемый период не всегда в полном объеме выполнялись требования инофирм.
Контроль технологии производства продукции проводится на комбинате:
- — постоянно — техническим контролем;
- — периодически — комиссионно.
Выявленные техническим контролем нарушения технологии производства регистрировали и оценивали. По каждому нарушению виновнику персонально выдавали талон «Предупреждение», а руководителю цеха — талон «Уведомление». По несоответствующей продукции применяли действия, указанные в разделе 13 и проводили корректирующие и предупреждающие действия (раздел 14).
По сравнению с 1995 годом в 1996 году уменьшилось количество нарушений технологии в ЦОиМ на 66,6%, в ЭСПЦ-2 на 25%, в СПЦ-1 на 16,4%.
Техническим контролем в 1997 году за нарушения технологии выдано на 259 талонов предупреждений меньше, чем в 1996 году.
За 1998 год выявлено нарушение технологии по сравнению с 1997 годом в ЦОиМ в 2.5 раза больше, в ЭСПЦ — на прежнем уровне, в СПЦ-1 — на 14.4% меньше.
Таблица 2.13 Уровень соблюдения технологии на ОЭМК, %.
Технологические этапы. | ||||
ЭСПЦ-2: Выплавка. | 88,3. | 91,58. | 96,73. | 96,58. |
Внепечная обработка. | 90,1. | 93,25. | 97,93. | 97,88. |
Разливка. | 91,3. | 95,32. | 98,01. | 97,85. |
СПЦ-1. | 88,3. | 94,40. | 98,36. | 84,20. |
Увеличение нарушений по технологии в ЦОиМ обусловлено ужесточением требований к окисленным окатышам по основности и массовой доле закиси железа, введением аттестации МОК по каждой установке.
Основные нарушения технологии — не выдерживается давление воды в зоне вторичного охлаждения МНЛЗ, температура металла, скорость разливки, время охлаждения металла под колпаком.
Мероприятия по улучшению качества производимой продукции Комплекс мероприятий по повышению качества продукции на комбинате разделяется на две группы, одну из которых составляют вопросы технического и технологического направлений, а другую — контрольные, организационные, вопросы подготовки нормативно-технической документации.
Разработку и совершенствование производственных процессов осуществляет техническое управление в соответствии с планом НИР, утвержденным главным инженером.
По каждой работе руководители работы составляют рабочие планы проведения исследований с указанием методики проведения, этапов работы, сроков выполнения и ответственного исполнителя.
Выполнение плана контролируется еженедельно техническим директором и раз в квартал главным инженером с оформлением протоколов.
В целях повышения качества продукции были проведены следующие экономически и технологически обоснованные мероприятия (1995 год — 9 мероприятий, 1996 г.- 11, 1997 г. — 8, 1998 г.- 17), (затраты за 1995 г. на их осуществление приведены в таблице):
- — производство офлюсованных окатышей в отделении окомкования, что позволило повысить их физико-механические характеристики, улучшить восстановимость в печах металлизации, понизить расходы концентрата, бентонита, природного газа в отделении металлизации и извести в ЭСПЦ-2;
- — перевод шахтных печей отделения металлизации на высокотемпературную технологию, что снизило склонность окатышей к возгоранию, повысило механическую прочность окатышей, увеличило выход экспортных окатышей, снизило расход природного газа на 2,4 м³ на тонну, повысило производительность шахтных печей на 7%;
- — ввод в ЭСПЦ-2 трайбаппаратов для подачи в жидкий металл проволоки с порошкообразным наполнителем, что позволило производить металл с регламентированным содержанием алюминия и серы и выполнить заказы зарубежных фирм, производящих детали методом горячей штамповки с последующей механической обработкой;
- — ввод в ЭСПЦ-2 в работу двух агрегатов комплексной обработки стали, позволило снизить содержание включений и газов в металле (массовой доли азота и кислорода на основном качественном сортаменте), что позволило производить металл с содержанием азота и кислорода не более 0,009 и 0,025% соответственно;
- — использование окалины сортопрокатного цеха при производстве окисленных окатышей позволило снизить расход концентрата на 8,5 кг на тонну без ухудшения их качества;
- — изменение режимов раскисления стали, повысило стабильность режимов разливки, что обеспечило снижение технологической обрези от 5 до 32 кг/т для различных сталей;
- — изменение режимов водоохлаждения НЛЗ и амплитуды колебаний на УНРС улучшило качество поверхности проката, что обеспечило снижение количества плавок низколегированных марок стали, дорабатываемых после обточки на 6,4%-12,6%;
- — внедрение дифференцированных режимов термообработки обеспечило снижение брака УЗК на 0,4%;
- — внедрение новой калибровки валков при производстве круга 100−120 мм и 150−160 мм позволило улучшить качество поверхности проката низколегированных марок стали, а также привело к снижению трудозатрат при отделке проката и снижению брака по поверхностным дефектам;
- — внедрение технологии совместного измельчения металлосодержащих отходов возврата окисленных и металлизованных окатышей. Это позволило в сравнении с 1996 годом снизить на 5,1 кг/т расход концентрата, всего 12,3 тыс. т; снизить расход окисленных окатышей на металлизованные на 10 кг/т, всего 17,3 тыс. т; сэкономить 11,4 м3/т природного газа. За 1997 год по сравнению с 1996 удельный расход огнеупоров был снижен на 5,654 кг/т, всего сэкономлено 9350 тонн; расход меди на кристаллизаторы снижен в 2,5 раза. Техобрезь снижена на 1,94 кг/т и на обрези сэкономлено 3210 тонн литой
в СПЦ-1 введен участок для осмотра и выборочной зачистки металла на участке обточки, внедрены подвесные наждачные зачистные машины на обводном рольганге, оптимизированы тепловые режимы нагрева металла, применены калибры с меньшими припусками под обточку, что позволило сэкономить в сравнении с 1996 годом 3400 тонн литой заготовки за счет с…
Мировой рынок подшипниковой стали достаточно специфичен. С одной стороны, практически каждый агрегат, автомобиль, любое изделие машиностроения имеет подшипник, и из-за этого потребление стали для изготовления подшипников стабильно растет. С другой — производители подшипников имеют определенных поставщиков стали, обеспечивающих в течение длительного времени баланс качества и цены.
ОЭМК давно занимается производством подшипниковой стали и на сегодняшний день является лучшим в СНГ производителем трубной и сортовой заготовки, предназначенной для изготовления колец подшипников. Достигнуты определенные успехи в производстве стали для роликов. На внутреннем рынке этот металл находит спрос, даже, несмотря на сокращение объемов производства машиностроительных заводов. Сейчас перед специалистами комбината встал вопрос расширения поставок подшипниковой стали на экспорт, а для этого необходимо достичь таких параметров качества, которые бы сравнялись с аналогичными показателями лучших заводов Японии, Западной Европы, Америки. Основная задача для ОЭМК — снижение содержания кислорода в стали. Его должно быть не более 0,0015, а в ряде случаев не более 0,0012 процента.
Сталеплавильная лаборатория техуправления совместно со специалистами ЭСПЦ разрабатывают комплекс технологических решений для выполнения поставленной задачи. Можно было бы воспользоваться мировым опытом, тем более, что это не секрет. Но технология на каждом заводе рассчитана под имеющееся оборудование, а значит просто скопировать ее с какого-то предприятия невозможно. Для этого нужна или глубокая модернизация, или реконструкция, но и то, и другое предполагает финансирование. Поэтому необходимо искать другие пути решения проблемы. В частности, необходимо отработать технологию на агрегатах комплексной обработки стали, усовершенствовать технологию вакуумирования стали, существенно изменить непрерывную разливку стали.
Необходимо закупить и внедрить в производство импортные корундографитовые стаканы, которые помогут решить вопросы по крупным неметаллическим включениям и улучшить структуру литой заготовки.
Результатом всех этих мероприятий является подшипниковая сталь, в которой содержание кислорода не превысило 0,0013%.Однако, кроме этого, еще предстоит сделать: внедрить принципиально другие шлаковые смеси для промежуточного ковша, стартовую засыпку шибера стальковша.
Таким образом, мы решаем нашу проблему и направляем свою работу в русло производства качественной продукции. Одним из перспективных направлений развития качественной металлургии является увеличение объема производства стали, обработанной внепечными способами, что позволяет улучшить ее качество, а также выплавлять сложный сортамент и в крупнотоннажных дуговых сталеплавильных печах (ДСП) /31/.
Таблица 3.1 Используемые данные для расчёта по цеху Эспц, в цехе используются 4 Дсп, 150 т
Исходные данные. | Значение. | Коэффициенты трудности. |
объем производства стали т. т/год. | ||
доля в общей выплавке подшипниковых сталей,%. | 26,0. | 1,20. |
углеродистых конструкционных качественных,%. | 14,0. | 1,12. |
легированных конструкционных качественных,%. | 48,0. | 1,15. |
трубных,%. | 8,0. | 1,17. |
углеродистых и низколегированных обычного качества. | 4,0. | 1,00. |
длительность плавки, часов. | 1,9. |
Затраты на заданное в производство в себестоимости 1 тонны стали соответственно 680; 700; 690; 695 руб/тонну. Расходы по переделу на 1 тонну (физическую) 540 руб. Количество и стоимость брака соответственно 0,008 т/т и 7 руб/т стали; потери от брака 8 руб/т. (Данные условные за 1997 год с учетом деноминации).
Работой предусмотрено внедрение установки внепечной вакуумной обработки стали. Данная технология включает: вакуумирование, десульфурацию и раскисление, выравнивание химического состава и температуры. Это позволяет снизить содержание серы с 0,02 до 0,005%, кислорода до 0,0013%, неметаллических включений на 0,17−0,27% и длительность плавки на 20%. Цех можно условно специализировать на выплавке подшипниковых сталей, углеродистых конструкционных качественных сталей, легированных конструкционных качественных сталей, трубных сталей (по 25% каждой от общего объема производства).
Долговечность подшипников в сфере их потребления увеличивается на 20% /31/.
Определим влияние внедрения внепечной обработки стали (ВОС) на показатели работы ДСП.
Средняя длительность плавки:
tср = t1*a1*k1+ t2*a2* k2 +…+ tn*an* kn, (10).
где t1, t2, …, tn — длительность плавки при выплавке стали соответствующих марок, час; a1, a2, …, an — доля стали различных марок в общей выплавке, k1, k2, …, kn — коэффициент трудности выплавки стали.
Средняя длительность плавки — до внедрения мероприятия: 1.9*1.0*0.04+1.9*1.2*0.26+1.9*1.15*0.48 + 1.9*1.12*0.14 + 1.9*1.17*0.08 = 2.17 (час).
За счет переноса части операций из печи в установки ВОС длительность плавки снижается на 20% и составит:
для подшипниковых сталей: 1.9*(1−0,2)*1,2=1,75 (ч);
для конструкционных углеродистых: 1,9*(1−0,2)*1,12=1,7 (ч);
для конструкционных легированных: 1,9*(1−0,2)*1,15=1,82 (ч);
для трубных: 1,9*(1−0,2)*1,17=1,78 (ч);
Средняя длительность плавки: 1,75*0,25+1,7*0,25+1,82*0,25+1,78*0,25 = 1,76 (час), где 0,25 — доля каждой стали в общей выплавке после внедрения мероприятия.
Изменение длительности плавки вызовет изменение других показателей работы печей. Их перечень и величины приведены в Приложении 3.
Масса выплавки увеличится из-за устранения брака и составит 142,7+0,008*142,7=144,85 (т), где 142,7 — масса плавки до внедрения, т; 0,008 — брак, т/т стали. Так как долю выплавляемых марок стали в общем объеме мы определяем в размере 25% каждого вида, то условно специализируем печь 1 на выплавке легированных конструкционных, печь 2 — на выплавке углеродистых конструкционных, печь 3 — на выплавке подшипниковых, а печь 4 — на выплавке трубных сталей.
Таким образом, показатели работы ДСП улучшаются. Объем производства стали увеличивается на 2242,4 — 1805,2 = 437,2 т. т, или на (+437 200/1805200)*100% = 24,2%.
Улучшается и комплексный показатель степени использования печей на 21,7 — 17,5 = 4,2 т /(МВА*сут), или на (4,2/17,5)*100% = 24,2%.
Определим влияние внедрения ВОС на показатели работы электросталеплавильного цеха.
Условно-годовая экономия от увеличения объема производства стали (достигаемого в результате снижения длительности плавки) 540*0,45*437,2=106 239,6 (тыс.руб), или 106 239,6/2242,4=47,4 (р/т), где 540 — расходы по переделу на 1 тонну стали, руб/т; 0,45 — доля условно-постоянных затрат; 437,2 — годовой прирост выплавки стали, тыс.тонн.
Условно-годовая экономия от снижения расхода ферросплава в результате внедрения ВОС 5000*0,003 = 15 руб/т стали, где 5000 — средняя цена за 1 т ферросплавов, руб/т; 0,003 — снижение их удельного расхода, т/т стали.
Общее снижение текущих затрат 47,4+ 15 + 8 = 70,4 (руб/т стали), где 8 — снижение потерь от брака, руб/т.
Принимаем, что дополнительные капитальные затраты составляют: на вакууматор и обслуживающее его оборудование 38 000 тыс. руб, агрегат комплексной обработки стали 52 000 тыс. руб.; дополнительные текущие затраты на ВОС 89 руб/т стали.
Себестоимость стали повышенного качества изменяется в среднем на -70,4 + 89,0 = +18,6 (руб/т) и составит 1318,8 +18,6 = 1337,4 (руб/т), где 1318,8 — средняя себестоимость до мероприятия, руб/т.
(680−7+540*1,15+8)*0,25 + (700−7+540*1,2+8)*0,25 + (690−7+540*1,12+8) + (695−7+540*1,17+8) = 1302*0,25+1349*0,25+1296*0,25+1328*0,25 = 1318,8 (руб/т), где 680; 700; 690; 695 — затраты на заданное в себестоимости соответственно конструкционных легированных, подшипниковых, конструкционных углеродистых, трубных сталей, руб/т; 1,15; 1,2; 1,12; 1,17 — коэффициенты трудности их выплавки; 0,25 — доля их выплавки; 540 — расходы по переделу на 1 тонну (физическую), руб; 7,0 — стоимость брака, руб/т; 1302; 1349; 1296; 1328 — себестоимость стали традиционного качества, руб/т.
Текущие затраты на производство стали увеличиваются в сталеплавильном производстве на 18,6*2242,4 = 41 708,6 (тыс.руб). Стоимость основных фондов цеха возрастет на 52 000 + 38 000 = 90 000 (тыс.руб) и составит 1 000 250 + 90 000 = 1 090 250 (тыс.руб), где 1 000 250 — стоимость основных фондов цеха до внедрения мероприятия.
Фондоотдача возрастет на 2 242 400/1090250 — 1 805 200/1000250 = 2,06 — 1,8 = 0,3 (т/тыс.руб), или на (0,3/1,8)*100% = 16,6%.
Производительность труда в цехе возрастет на 2 242 400/1480−1 805 200/1471=1515,2 -1227,2 = 288,2 (т/чел), или (288,2/1227,2)*100% = 23,5%.
Обобщающим показателем эффективности производства отдельного вида продукции является ее рентабельность.
Рентабельность производства конструкционных легированных стали до внедрения мероприятия: ((1432−1302)/1302)*100% = 9,9%, для стали нового качества: (((1432+48,6)-(1302+18,6))/1320,6)*100% = 12,1%. Увеличение рентабельности составило 2,2%;
Рентабельность производства подшипниковых сталей до внедрения мероприятия: ((1500−1349)/1349)*100% = 11,2%, для стали нового качества: (((1500+50)-(1349+18,6))/1367,6)*100% = 13,3%. Увеличение рентабельности 2,1%.
Рентабельность производства конструкционной углеродистой стали до мероприятия: ((1430−1296)/1296)*100% = 10,34%, для стали нового качества: (((1430+48,6)-(1296+18,6))/1314,6)*100% = 12,5%. Увеличение рентабельности 2,2%.
Рентабельность трубных сталей до мероприятия: ((1468−1328)/1328)*100%= 10,5%, для стали нового качества: (((1468+49,4)-(1328+18,6))/1346,6)*100% =12,7%. Увеличение рентабельности 2,2%.
В расчетах используются следующие данные (соответственно для каждого варианта): 1432, 1500, 11 430, 1468 — оптовая цена стали; 48,6; 50,0; 48,6; 49,4 — приплаты, руб/т; 18,6 — дополнительные текущие затраты на ВОС, руб/т; 1302; 1349; 1296; 1328 — себестоимость 1 тонны стали по вариантам, руб/т.
Таким образом, средняя рентабельность производства стали до внедрения мероприятия 10,5%, после — 12,7%, прирост +2,2%.
Определим влияние ВОС ни изменение показателей работы предприятия.
В прейскуранте оптовых цен предусмотрены приплаты за снижение содержания серы с 0,03 до 0,005%, кислорода до 0,0013% - в размере 2% к оптовой цене; 20,0 руб/т — за 1 т вакуумированной стали.
Для подшипниковых сталей приплаты за снижение содержания серы и кислорода составят 1432*0,02 = 28,64 (руб/т), где 1432 — оптовая цена, руб/т. Приплаты за улучшение качества подшипниковых сталей 28,64 + 20,0 = 48,64 (руб/т), или 48,64*564,3 = 27 424,9 (тыс. руб) на их годовое производство.
Для конструкционных легированных сталей размер приплат определяем аналогично (500*0,02+20)*580,9 = 29 045 (тыс. руб).
Для конструкционных углеродистых сталей размер приплат: (1430*0,02+20)*542,5 = 26 365,5 (тыс. руб).
Для трубных — (1468*0,02+20)*654,7 = 27 402,2 (тыс. руб).
Сумма приплат 110 237,1 (тыс. руб).
Прирост прибыли предприятия за счет улучшения качества стали при внепечной обработке 110 237,1 — 18,6*2242,4 = 68 528,5 (тыс.руб), где 18,6 — увеличение себестоимости стали, руб/т.
Срок окупаемости дополнительных капитальных затрат на ВОС:
90 000/68528,5 = 1,3 года или 1 год и 4 месяца.
Результаты проведенных расчетов приведены в таблице 3.2.
Таблица 3.2 Эффективность внедрения установки внепечной вакуумной обработки стали в ЭСПЦ
Показатели. | До внедрен. | После внедрен. | Измен., %. |
Длительность плавки, час. | 2,17. | 1,76. | +22,0. |
Масса плавки, тонн. | 142,70. | 143,85. | +0,8. |
Годовая выплавка стали, т. т. | 1805,20. | 2242,40. | +24,2. |
Себестоимость 1 т стали, руб/т. | 1318,10. | 1337,40. | +1,5. |
Фондоотдача, т/1000 руб. | 1,80. | 2,06. | +16,6. |
Производительность труда, т/чел. | 1272,20. | 1515,20. | +23,5. |
Рентабельность, %. | 10,50. | 12,70. | 2,2. |
Прирост прибыли за счет улучшения качества стали, тыс. руб. | 68 528,5. | ||
Срок окупаемости, лет. | 1,3. |