Основное оборудование сульфатного отделения
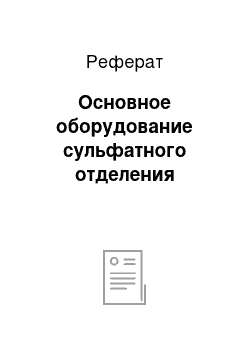
Во втором случае возможен форсированный режим работы аппарата при высоких тепловых нагрузках, так как кипение раствора в трубчатке существенно интенсифицирует теплоотдачу. Однако при таком режиме возрастает вероятность пристеночного солеобразования в трубчатке, а также чрезмерного зародышеобразования при повышенном пересыщении раствора. Оптимальный режим работы нагревателя 1 предполагает… Читать ещё >
Основное оборудование сульфатного отделения (реферат, курсовая, диплом, контрольная)
К основному оборудованию сульфатного отделения цеха улавливания относятся: абсорбер, вакуум-выпарной кристаллизатор, центрифуга.
При бессатураторном методе получения сульфата аммония очистку газа от аммиака осуществляют в двухступенчатом абсорбере оросительного типа, представленном на рис. 5.15 [33] в разрезе с сечениями на уровне разделительной тарелки и отбойника.
Корпус аппарата состоит из цилиндрической обечайки 4, конического днища 5 и крышки 1. Внутреннее пространство аппарата разделено на две секции посредством кольцевой перегородки с обечайкой 10, в верхней части которой смонтирована (строго горизонтально) колпачковая барботажная тарелка с кольцевым переливом на уровне кромок обечайки 10. Штуцеры 3, а также установленные над ними колпаки 11 имеют трапециидальную форму и на тарелке расположены радиально, как показано на сечении А-А.
Внутри обечайки 10 установлен каплеотбойник 9, выполненный из изогнутых полос листового материала (см. сечение а-а). Верхняя и нижняя секции абсорбера оборудованы индивидуальными системами орошения и выполняют функции первой и второй ступени абсорбции аммиака. Нижняя секция (первая ступень) оборудована двумя ярусами форсунок 8 по шесть штук в каждом. Верхняя секция (вторая ступень) имеет один ярус форсунок 12, кроме того, вдоль оси аппарата расположена форсунка 13 с крупнокапельным орошением, предназначенная также для уменьшения брызгоуноса газовым потоком. Верхняя секция оборудована люками 2.

Рисунок 2.2 Аммиачный абсорбер: 1 — крышка, 2-люк, 1 — патрубок для входа газа, 3 — штуцер колпачковой тарелки, 4 — цилиндрическая обечайка 5 — коническое днище, 6,15 — патрубки для вывода раствора, 7 — штуцер входа газа, 8,12,13 — форсунки, 9 — каплеотбойник, 10 — обечайка, 11 — колпак, 14 — патрубок для выхода газа.
Коксовый газ поступает в нижнюю секцию аппарата через патрубок 7, промывается кислым раствором циркуляционного цикла первой ступени абсорбции посредством форсунок 8, затем освобождается от брызг раствора в каплеотбойнике 9 и поступает в штуцеры 3 колпачковой тарелки, которая заполнена жидкостью до уровня кромок обечайки 10. При этом в нижней секции абсорбера из газа извлекается около 95% содержащегося в нем аммиака.
Циркулирующий раствор кислотностью около 1% после контакта с газом поступает в коническое днище 5 и выводится через патрубок 6.
Вход газа в верхнюю секцию абсорбера осуществляется в режиме барботажа благодаря наличию погруженных в жидкость колпаков 11. Далее газ подвергается повторному контактированию с жидкой фазой в режиме орошения посредством форсунок 12 и 13. В процессе рециркуляции в контуре оросительной системы второй ступени раствора кислотностью 10- 12% из газа извлекаются остатки аммиака и легкие пиридиновые основания. Очищенный коксовый газ выводится из абсорбера через патрубок 14, а раствор накапливается в кольцевом зазоре между стенками абсорбера и обечайки 10 и выводится через патрубок 15.
Технические характеристики абсорбера:
Производительность по газу…100 000 м3/ч Количество раствора на орошение каждой ступени (секции)…380 м3/ч Диаметр…3600 мм Площадь свободного сечения (с учетом футеровки)… 8,5 м2
Скорость газа в свободном сечении аппарата…3м/с Масса аппарата… ~32т Получение кристаллического сульфата аммония путем переработки ненасыщенного питающего раствора, выводимого из первой ступени аммиачного абсорбера, осуществляется в выпарном кристаллизаторе (рис. 2.3).
Корпус аппарата имеет цилиндрическую форму. Полая часть его состоит из секций 3 и 4 различного диаметра, причем секция 3 частично заполняется раствором, уровень которого визуально контролируется посредством смотровых окон 10. Секция 3 стыкуется посредством фланцевого соединения с верхней трубной решеткой нагревателя 1, в центральной части которого расположена циркуляционная труба 2, а в периферийной части — вертикальная трубчатка. Верхняя часть нагревателя 1 оборудована кольцевым коллектором с патрубком 7 для подачи греющего пара, а в нижней части установлен патрубок 9 для вывода конденсата. Нижняя трубная решетка нагревателя 1 посредством фланцевого соединения стыкуется с коническим днищем, в котором имеется люк — лаз (на рисунке не показано), патрубок 5 для подачи питающего раствора и труба 6 для вывода продуктовой суспензии.
Секция 4 снабжена системой каплеотбоя в виде наклонно установленных полок и патрубком 8 для вывода вторичного пара.
В процессе работы в выпарном кристаллизаторе поддерживается постоянный уровень раствора путем регулирования расхода питающего раствора на входе в патрубок 5. В зоне конического днища аппарата питающий раствор смешивается с циркулирующим раствором, поступающим из трубы 2. Циркулирующий раствор содержит кристаллическую фазу и на выходе из трубы 2 имеет остаточное пересыщение, которое снижается или полностью снимается в результате смешения с питающим раствором. После смешения раствор поступает в трубчатку нагревателя 1.
В результате конденсации пара в межтрубном пространстве нагревателя 1 находящийся в трубчатке раствор получает соответствующее количество тепла. В зависимости от высоты уровня раствора над верхней трубной решеткой, который определяет величину гидростатического давления жидкости в верхней части трубчатки, получаемое раствором тепло расходуется в определенном соотношении на повышение его температуры или на испарение воды непосредственно в трубчатке. Это обстоятельство определяет два возможных режима работы нагревателя 1:
¦ при увеличенном уровне раствора в аппарате в трубчатке преобладает режим конвективного подогрева раствора с последующим его кипением вне трубчатки по мере подъема раствора и снижения гидростатического давления;
¦ при минимальном уровне раствора относительно верхней трубной решетки процесс теплопередачи сопровождается кипением раствора непосредственно в трубчатке.
Во втором случае возможен форсированный режим работы аппарата при высоких тепловых нагрузках, так как кипение раствора в трубчатке существенно интенсифицирует теплоотдачу. Однако при таком режиме возрастает вероятность пристеночного солеобразования в трубчатке, а также чрезмерного зародышеобразования при повышенном пересыщении раствора. Оптимальный режим работы нагревателя 1 предполагает обеспечение таких условий вы Для получения крупнокристаллического сульфата аммония улучшенного фракционного состава применяются кристаллизаторы со взвешенным слоем частиц и внешним контуром циркуляции раствора, снабженным подогревателем парной кристаллизации, которые гарантируют получение Рис. 5.16. крупнокристаллического продукта при непрерывной рабоВакуум-кристаллизатор те аппарата между его промывками в течение 3 суток. Кипение раствора в периферийной части сечения аппарата сопровождается его пересыщением и создает нисходящий поток в трубе 2 и восходящий в трубчатке нагревателя 1, то есть циркуляцию суспензии кристаллов по замкнутому контуру. Многократное прохождение кристаллов через зону образования пересыщения (зону кипения) обеспечивает их рост и накопление массы твердой фазы в циркуляционном контуре. Непрерывный вывод суспензии с постоянной объемной скоростью по трубе б обеспечивает постоянство массы твердой фазы в выпарном кристаллизаторе на оптимальном уровне.

Рисунок 2.2 — Вакуум-выпарной кристаллизатор: I — нагреватель трубчатый; 2 — труба циркуляционная; 3 — испарительная секция; 4 — каплеотбойная секция; 5 — вход раствора; 6 — выход пульпы; 7 — вход греющего пара; 8 — выход вторичного пара; 9 — выход конденсата; 10-смотровые окна
Образовавшаяся в процессе кипения раствора паровая фаза проходит каплеотбойную секцию 4, где освобождается от уносимых брызг раствора, и выводится через патрубок 8 на конденсацию. Для снижения температуры кипения раствора в выпарном кристаллизаторе поддерживается соответствующий вакуум.
Технические характеристики выпарного кристаллизатора:
Габариты аппарата:
Диаметр…2,7 м Высота…8,5 м Диаметр труб нагревателя…57×4мм.
Поверхность теплопередачи (по внутреннемудиаметру труб)…246м.
Диаметр центральной циркуляционной трубы (по внутренним.
стенкам)…620мм.
Номинальный вакуум в объеме аппарата…685 мм рт. ст Температура раствора в объеме аппарата…55 — 65 °C Температура греющего пара…125−130°С Окончательное выделение продуктовых кристаллов сульфата аммония из растворного цикла сульфатной установки обеспечивается путем фильтрования суспензии через металлическую перфорированную перегородку с последующим отжимом остатков маточного раствора и промывкой осадка горячей технической водой под воздействием центробежного фактора. Для этих целей применяются автоматические горизонтальные центрифуги с пульсирующей выгрузкой осадка типа ½ ФГП. На рис. 2.3 приведена конструктивная схема ротора центрифуги. Полый вал 4 опирается на подшипники 3 и жестко соединен одним концом с полым шкивом 2, а другим — с перфорированным цилиндром 9 (наружный каскад ротора), ко дну которого посредством стоек 8 жестко крепится выталкивающее кольцо 14 с приемным конусом 11. Все указанные элементы конструкции совершают только вращательное движение посредством шкива 2. Полый вал 4 снабжен втулками 6, в отверстиях которых скользяще установлен шток 5, снабженный на одном конце поршнем, перемещающимся в цилиндрической полости шкива 2, а на другом — перфорированным цилиндром 10 (внутренний каскад ротора), который крепится к штоку 5 днищем.
Устройство 1 для подачи масла в цилиндрическую полость шкива 2, а также поршень штока 5 представляют собой гидропривод, обеспечивающий возвратно-поступательное перемещение перфорированного цилиндра 10 (вместе со штоком 5) вдоль-оси ротора центрифуги. Наряду с этим цилиндр 10 и шток 5 с поршнем, жестко связанные между собой, совершают вращательное движение синхронно вращению перфорированного цилиндра 9 с валом 4 и шкивом 2 Суспензия из вращающегося приемного конуса 11 поступает в кольцевую пристеночную зону.

Рисунок 2.2 Конструктивная схема центрифуги типа ½ ФГП: 1- устройство для подачи масла; 2 — шкив; 3 — подшипники; 4 — 5 — шток; 6 — втулка; 7 — кожух; 8 — стойка; 9 — перфорированный цилиндр (наружный каскад ротора); 10- перфорированный цилиндр (внутренний каскад ротора); 11- приемный конус; 12 — труба для промывки слоя осадка; 13 — сменное кольцо; 14 — выталкивающее кольцо цилиндра 10 (ограниченную кромками кольца 14 и конуса 11), образуя первичный слой кристаллического осадка вследствие фильтрации жидкой фазы сквозь перфорацию цилиндра 10, на стенках которого уже имеется отфильтрованный вторичный слой на участке цилиндрической поверхности между кромками конуса 11 и цилиндра 10. В то же время на перфорированных стенках вращающегося цилиндра 9 также содержится слой кристаллического осадка, ширина которого соответствует расстоянию между кромками цилиндров 9 и 10 по образующей. При перемещении цилиндра 10 влево кольцо 14 подпирает первичный и вторичный слои осадка, вследствие чего часть вторичного слоя под воздействием центробежной силы перемещается со стенок цилиндра 10 на стенки цилиндра 9.
При перемещении цилиндра 10 вправо в кольцевой пристеночной зоне вследствие непрерывной подачи суспензии в конус 11 вновь образуется первичный слой кристаллического осадка, и одновременно кромка цилиндра 10 сталкивает часть вторичного слоя со стенок цилиндра 9, а центробежная сила обеспечивает его срез по кромке ротора центрифуги.
Ротор центрифуги расположен в кожухе 7, в нижней части которого расположены каналы для раздельного вывода фильтрата и влажных кристаллов. Заданная толщина вторичного слоя осадка в цилиндре 10 устанавливается посредством сменного кольца 13. Для промывки слоя осадка предусмотрена труба 12.
Технические характеристики центрифуг, применяемых в сульфатных отделениях:
Типоразмер центрифуг…½ФГП-630 ½ФГП-800.
Внутренний диаметр каскада ротора, мм…630 800.
Фактор разделения…595 644.
Максимальная производительность по осадку.
сульфата аммония, кг/ч…2500 8000.
Мощность привода общая, кВт… 33 52.
Удельная материалоемкость, кг/(кг/ч)…0,88 0,75.
Удельная энергоемкость, кВт/(кг/ч)…0,013 0,006.
Эффективная работа центрифуг обеспечивается при концентрации твердой фазы в суспензии 40 — 50% (по массе) и содержании в твердой фазе частиц размером более 100мкм не менее 90%.