Получение заготовок из пластмасс
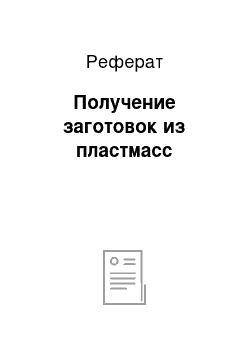
Экструдер (рис. 8.12, а) состоит из нескольких основных узлов: корпуса 3, оснащенного нагревательными элементами 4; рабочего органа (шнека, диска, поршня) 2, размещенного в корпусе; узла загрузки перерабатываемого материала 1; силового привода; системы задания и поддержания температурного режима, других контрольно-измерительных и регулирующих устройств. Основной рабочий орган экструдеров… Читать ещё >
Получение заготовок из пластмасс (реферат, курсовая, диплом, контрольная)
В большинстве случаев пластмассовые детали получают способами прессования, литья, выдавливания.
Прямое (компрессионное) прессование
Это один из основных способов получения деталей из реактопластов.
В полость матрицы 3 (рис. 8.7, а) загружают предварительно гранулированный или порошкообразный материал 2. При замыкании пресс-формы под действием силы пресса пуансон 1 создает давление на материал (рис. 8.7, б). Под действием этого давления и теплоты от нагретой прессформы материал размягчается и заполняет формообразующую полость. После определенной выдержки, необходимой для отверждения материала, пресс-форму раскрывают и с помощью выталкивателя 5 извлекают готовую деталь 4 (рис. 8.7, в). Внешний вид пресс-формы показан на рис. 8.8.

Рис. 8.7. Схемы прямого прессования:
а — засыпка в пресс-форму материала; б — момент прессования; в — момент распрессовки; 1 — пуансон; 2 — гранулированный материал; 3 — матрица; 4 — готовая деталь; 5 — выталкиватель.

Рис. 8.8. Пресс-форма для получения пластмассовых деталей.
Процесс отверждения сопровождается выделением летучих составляющих композиционного материала и паров влаги. Для удаления газов выполняют так называемую подпрессовку, заключающуюся в переключении гидропресса после определенной выдержки на обратный ход, подъеме пуансона на 5−10 мм и выдержке его в таком положении в течение 2−3 с. После этого прессформу снова смыкают.
Температура и давление прессования зависят от вида перерабатываемого материала, формы и размеров изготовляемой детали. Время выдержки под прессом зависит от скорости отверждения и толщины прессуемой детали. Для большинства реактопластов его выбирают из расчета 0,5−2 мин на 1 мм толщины стенки. Технологическое время может быть сокращено вследствие предварительного подогрева материала в специальных шкафах.
Прямым прессованием получают детали средней сложности и небольших размеров из термореактивных композиционных материалов с порошкообразным и волокнистым наполнителями.
Литьевое прессование
При методе литьевого прессования исходный термореактивный материал 1 загружают в специальную обогреваемую загрузочную камеру 3 (рис. 8.9).

Рис. 8.9. Схема литьевого прессования:
1 — термореактивный материал; 2 — пуансон; 3 — загрузочная камера; 4, 6 — половинки пресс-формы; 5 — готовая деталь Под действием теплоты он переходит в вязкотекучее состояние и под давлением пуансона 2 выжимается в полость матрицы пресс-формы через специальное отверстие в литниковой плите.
После отверждения прессформу разъединяют и готовую деталь 5 извлекают из матрицы. Литьевое прессование позволяет получать детали сложной формы. В случае необходимости готовые изделия подвергают отделке — обрезке по контуру, удалению заусенцев, нанесению покрытий, термообработке.
Литье под давлением
Литье под давлением является высокопроизводительным и эффективным способом массового производства деталей из термопластов.
Перерабатываемый материал из загрузочного бункера 8 (рис. 8.10) подается дозатором 9 в рабочий цилиндр 6 с электронагревателем 4.

Рис. 8.10. Схема литья под давлением:
1 — пресс-форма; 2 — изготовляемая деталь; 3 — сопло; 4 — нагревательный элемент; 5 — рассекатель; 6 — рабочий цилиндр; 7 — поршень; 8 — бункер; 9 — дозатор При движении поршня 7 определенная доза материала поступает в зону обогрева, а уже расплавленный материал через сопло 3 и литниковый канал попадает в полость пресс-формы 1, в которой формируется деталь 2. В рабочем (нагревательном) цилиндре на пути потока расплава установлен рассекатель 5, который заставляет его протекать тонким слоем у стенок цилиндра. Это ускоряет прогрев и обеспечивает более равномерную температуру расплава. При движении поршня в исходное положение с помощью дозатора 9 очередная порция материала подается в рабочий цилиндр. Для предотвращения перегрева выше 50−70°С в процессе литья пресс-форму охлаждают проточной водой. После охлаждения материала ее размыкают и с помощью выталкивателей извлекают готовую деталь. Широко применяют также литьевые машины с червячной пластикацией материала, в которых вместо поршня используют вращающиеся червяки. Внешний вид одной из моделей показан на рис. 8.11.

Рис. 8.11. Оборудование для литья под давлением пластмасс.
Литьем под давлением получают детали сложной конфигурации с различными толщинами стенок, ребрами, резьбами и т. д. Производительность литья в 20−40 раз выше прессования. Качество отливаемых деталей зависит от температур пресс-формы и расплава, давления прессования, продолжительности выдержки под давлением и т. д.
Центробежное литье. Его применяют для получения крупногабаритных и толстостенных деталей. Центробежные силы прижимают залитый в форму полимерный материал к ее внутренней поверхности. После затвердения готовую деталь извлекают и заливают новую порцию расплавленного полимера.
Экструзия
Экструзией называется процесс переработки материалов в экструдере. Экструдер (от лат. extrudo — выталкиваю) — оборудование для пластикации материалов и придания им формы путем продавливания через профилирующий инструмент, сечение которого соответствует конфигурации изделия. В нем получают главным образом изделия из термопластичных полимерных материалов: пленки, листы, трубы, шланги, изделия сложного профиля и др.
Экструдер (рис. 8.12, а) состоит из нескольких основных узлов: корпуса 3, оснащенного нагревательными элементами 4; рабочего органа (шнека, диска, поршня) 2, размещенного в корпусе; узла загрузки перерабатываемого материала 1; силового привода; системы задания и поддержания температурного режима, других контрольно-измерительных и регулирующих устройств. Основной рабочий орган экструдеров выполняют как одно-, так и многошнековым.

Рис. 8.12. Непрерывное выдавливание:
а — схема установки; 6 — профили получаемых деталей Захватывая исходный материал (гранулы, порошок, ленту и др.) из загрузочного устройства 1, шнек 2 перемещает его вдоль корпуса. При этом материал сжимается, давление в экструдере достигает 15−50 МПа. В результате передачи теплоты от нагревательного элемента 4 и выделения ее при трении частиц друг о друга и о стенки цилиндра перерабатываемый материал переходит в вязкотекучее состояние, гомогенизируется. Далее расплавленный материал проходит через радиальные канавки оправки 5 и выдавливается через калиброванное отверстие головки 6. Оправку применяют для получения отверстия при производстве труб. Непрерывным выдавливанием можно изготовлять детали различного профиля (рис. 8.12, б). Внешний вид современного экструдера показан на рис. 8.13.

Рис. 8.13. Внешний вид установки (а); реальный процесс экструзии (б):
1 — фильера; 2 — получаемый профиль.