Материаловедение и технология конструкционных материалов
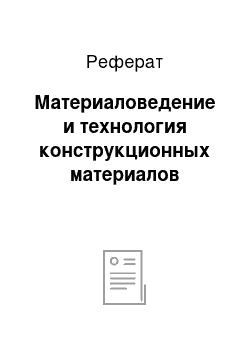
С целью экономии дефицитного вольфрама разрабатываются безвольфрамовые металлокерамические твердые сплавы на основе карбидов, а также карбидонитридов переходных металлов, в первую очередь титана, ванадия, ниобия, тантала. Эти сплавы изготовляют на никелемолибденовой связке. Полученные твердые сплавы на основе карбидов по своим характеристикам примерно равноценны стандартным сплавам группы ТК… Читать ещё >
Материаловедение и технология конструкционных материалов (реферат, курсовая, диплом, контрольная)
сплав сталь термический износостойкий Материаловедение — междисциплинарный раздел науки, изучающий изменения свойств материалов как в твёрдом, так и в жидком состоянии в зависимости от некоторых факторов. К изучаемым свойствам относятся: структура веществ, электронные, термические, химические, магнитные, оптические свойства этих веществ. Материаловедение можно отнести к тем разделам физики и химии, которые занимаются изучением свойств материалов. Кроме того, эта наука использует целый ряд методов, позволяющих исследовать структуру материалов. Изготовление наукоёмких изделий в промышленности, особенно при работе с объектами микрои наноразмеров необходимо детально знать характеристику, свойства и строение материалов… Решить эти задачи и призвана наука — материаловедение.
Знание структуры и свойств материалов приводит к созданию принципиально новых продуктов и даже отраслей индустрии. Однако и классические отрасли также широко используют знания, полученные учёными-материаловедами для нововведений, устранения проблем, расширения ассортимента продукции, повышения безопасности и понижения стоимости производства. Эти нововведения были сделаны для процессов литья, проката стали, сварки, роста кристаллов, приготовления тонких плёнок, обжига, дутья стекла и др. В этой работе мы постараемся вникнуть в суть этого предмета и применить на примерах, актуальных для нашей специальности, полученные нами знания.
1. Что представляют собой твердые растворы замещения и внедрения? Приведите примеры
Твердыми растворами называют фазы, в которых один из компонентов сплава сохраняет свою кристаллическую решетку, а атомы других (или другого) компонентов располагаются в решетке первого компонента (растворителя), изменяя ее размеры (периоды). Таким образом, твердый раствор, состоящий из двух или нескольких компонентов, имеет один тип решетки и представляет собой одну фазу. Существуют твердые растворы внедрения и твердые растворы замещения. При образовании твердых растворов внедрения атомы растворенного компонента B размещаются между атомами растворителя A в его кристаллической решетке. При образовании твердых растворов замещения атомы растворенного компонента B замещают часть атомов растворителя в его кристаллической решетке.
Рисунок 1 — Твердые растворы: а — замещения, б — внедрения Поскольку размеры растворенных атомов отличаются от размеров атомов растворителя, то образование твердого раствора сопровождается искажением кристаллической решетки растворителя.
Твердые растворы замещения могут быть с ограниченной и неограниченной растворимостью. В твердых растворах с ограниченной растворимостью концентрация растворенного компонента возможна до определенных пределов.

Рисунок 2 — Искажения кристаллической решетки в твердых растворах замещения: а — атом растворенного компонента больше атома растворителя, б — атом растворенного компонента меньше атома растворителя В твердых растворах с неограниченной растворимостью возможна любая концентрация растворенного компонента (от 0 до 100%). Твердые растворы с неограниченной растворимостью образуются при соблюдении следующих условий:
- 1) у компонентов должны быть однотипные кристаллические решетки;
- 2) различие в атомных радиусах компонентов не должно превышать для сплавов на основе железа 9%, а для сплавов на основе меди 15%;
- 3) компоненты должны обладать близостью физико-химических свойств. Однако соблюдение этих свойств не всегда приводит к образованию твердых растворов замещения с неограниченной растворимостью. На практике, как правило, образуются твердые растворы с ограниченной растворимостью.
Твердые растворы внедрения могут быть только с ограниченной концентрации, поскольку число пор в решетке ограничено, а атомы основного компонента сохраняются в узлах решетки.
Твердые растворы замещения с неограниченной растворимостью на основе компонентов: Ag и Au, Ni и Cu, Moи W, V и Ti, и т. д.
Твердые растворы замещения с ограниченной растворимостью на основе компонентов: Al и Cu, Cu и Zn, и т. д. Твердые растворы внедрения: при растворении в металлах неметаллических элементов, как углерод, бор, азот и кислород. Например: Fe и С.
2. Вычертите диаграмму состояния железо-карбид железа, укажите структурные составляющие во всех областях диаграммы, опишите превращения и постройте кривую охлаждения (с применением правила фаз) для сплава, содержащего 0,8% С. Какова структура этого сплава при комнатной температуре и как такой сплав называется?
Первичная кристаллизация сплавов системы железо-углерод начинается по достижении температур, соответствующих линии ABCD (линии ликвидус), и заканчивается при температурах, образующих линию AHJECF(линию солидус).
При кристаллизации сплавов по линии АВ из жидкого раствора выделяются кристаллы твердого растворауглерода в б-железе (д-раствор). Процесс кристаллизации сплавов с содержанием углерода до 0,1% заканчивается по линии АН с образованием б (д)-твердого раствора. На линии HJB протекает перитектическое превращение, в результате которого образуется твердый раствор углерода в г-железе, т. е. аустенит. Процесс первичной кристаллизации сталей заканчивается по линии AHJE.
При температурах, соответствующих линии ВС, из жидкого раствора кристаллизуется аустенит. В сплавах, содержащих от 4,3% до 6,67% углерода, при температурах, соответствующих линии CD, начинают выделяться кристаллы цементита первичного. Цементит, кристаллизующийся из жидкой фазы, называется первичным. B точке С при температуре 1147 °C и концентрации углерода в жидком растворе 4,3% образуется эвтектика, которая называется ледебуритом. Эвтектическое превращение с образованием ледебурита можно записать формулой.
ЖР4,3Л[А2,14+Ц6,67].
Процесс первичной кристаллизации чугунов заканчивается по линии ECF образованием ледебурита.
Превращения, происходящие в твердом состоянии, называются вторичной кристаллизацией. Они связаны с переходом при охлаждении г-железа в б-железо и распадом аустенита.
Линия GS соответствует температурам начала превращения аустенита в феррит. Ниже линии GS сплавы состоят из феррита и аустенита.
Линия ЕS показывает температуры начала выделения цементита из аустенита вследствие уменьшениярастворимости углерода в аустените с понижением температуры. Цементит, выделяющийся из аустенита, называется вторичным цементитом.
В точке S при температуре 727 °C и концентрации углерода в аустените 0,8% образуется эвтектоидная смесьсостоящая из феррита и цементита, которая называется перлитом. Перлит получается в результате одновременного выпадения из аустенита частиц феррита и цементита. Процесс превращения аустенита в перлит можно записать формулой.
А0,8П[Ф0,03+Ц6,67].
Линия PQ показывает на уменьшение растворимости углерода в феррите при охлаждении и выделении цементита, который называется третичным цементитом.
Следовательно, сплавы, содержащие менее 0,008% углерода (точка Q), являются однофазными и имеют структуру чистого феррита, а сплавы, содержащие углерод от 0,008 до 0,03% - структуру феррит + цементит третичный и называются техническим железом.
Доэвтектоидные стали при температуре ниже 727єС имеют структуру феррит + перлит и заэвтектоидные — перлит + цементит вторичный в виде сетки по границам зерен.
В доэвтектических чугунах в интервале температур 1147−727єС при охлаждении из аустенита выделяется цементит вторичный, вследствие уменьшения растворимости углерода (линия ES). По достижении температуры 727єС (линия PSK) аустенит, обедненный углеродом до 0,8% (точка S), превращаясь в перлит. Таким образом, после окончательного охлаждения структура доэвтектических чугунов состоит из перлита, цементита вторичного и ледебурита превращенного (перлит + цементит).
Структура эвтектических чугунов при температурах ниже 727єС состоит из ледебурита превращенного. Заэвтектический чугун при температурах ниже 727єС состоит из ледебурита превращенного и цементита первичного.
3. С помощью диаграммы состояния железо-карбид железа и графика зависимости твердости от температуры отпуска назначьте режим термической обработки (температуру закалки, охлаждающую среду и температуру отпуска) изделий из стали 50, которые должны иметь твердость 230…250 НВ. Опишите микроструктуру и свойства стали 50 после термической обработки
Критические точки для Ст50: АС1=725єС, АС3=760єС.
При нагреве до 700єС в стали 50 не происходят аллотропические превращения и мы имеем ту же структуру — перлит + феррит, быстро охлаждая (т.к. закалка), имеем также после охлаждения перлит + феррит с теми же механическими свойствами (примерно), что и в исходном состоянии до нагрева под закалку.
Если доэвтектоидную сталь нагреть выше Ас1, но ниже Ас3, то в ее структуре после закалки наряду с мартенситом будут участки феррита. Присутствие феррита как мягкой составляющей снижает твердость сталипосле закалки. Такая закалка называется неполной. Она обеспечивает хорошие механические свойства иштампуемость. При температуре нагрева структура — аустенит + феррит. При охлаждении со скоростью выше критической происходит мартенситное превращение: гМ. В результате получаем структуру феррит + мартенсит.
Оптимальный режим нагрева под закалку для доэвтектоидных сталей (%С<0,8%) составляет АС3+(30ч50є), т. е. для Ст50 — 800−820єС. При этом после закалки имеем мелкое зерно, обеспечивающее наилучшие механические свойства стали 50.
Нагрев и выдержка стали 50 выше температуры 820єС перед закалкой приводит к росту зерна и ухудшению механических свойств стали после термической обработки. Крупнозернистая структура вызывает повышенную хрупкость стали.
Для обеспечения скорости охлаждения выше критической в качестве среды охлаждения выбираем воду. Структура стали 50 при температуре нагрева под закалку — аустенит, после охлаждения со скоростью выше критической — мартенсит.
Отпуском называется нагрев стали до температуры ниже Ас1, выдержка при заданной температуре и последующее охлаждение с заданной скорость (обычно на воздухе). Отпуск является конечной операцией термической обработки, проводится после закалки для уменьшения внутренних напряжений и получения более равновесной структуры. Напряжения в закаленных изделиях снимаются тем полнее, чем выше температура отпуска.
Для получения твердости 230…250 НВ при диаметре заготовки 20 мм отпуск стали 50 необходимо проводить при температуре 500єС. Среда охлаждения — вода. При высокотемпературном отпуске образуется структура, которая называется сорбит отпуска. Сорбит отпуска состоит из ферритной основы, пронизанной частицами цементита.
Свойства стали 50 после термической обработки: ут=680−780 МПа, ув=870−970 МПа, д=13−11%, ш=61−57%, ан=120−80, НВ=230−250.

Рисунок 3 — диаграмма железо-цементит Правило фаз устанавливает зависимость между числом степеней свободы, числом компонентов и числом фаз и выражается уравнением:
C = K + 1 — Ф, где С — число степеней свободы системы;
К — число компонентов, образующих систему;
1 — число внешних факторов (внешним фактором считаем только температуру, так как давление за исключением очень высокого мало влияет на фазовое равновесие сплавов в твердом и жидком состояниях);
Ф — число фаз, находящихся в равновесии.
Сплав железа с углеродом, содержащий 0,8%С, называется эвтектоидной сталью. Его структура при комнатной температуре — перлит.
- 4. В результате термической обработки шестерни должны получить твердый износоустойчивый поверхностный слой при вязкой сердцевине. Для их изготовления выбрана сталь 12ХН3А. Укажите состав и определите группу стали по назначению. Назначьте режим термической и химико-термической обработки, приведите его обоснование, объяснив влияние легирования на превращения, происходящие на всех этапах обработки данной стали. Опишите структуру и свойства стали после термической обработки
- 12ХН3А сталь — конструкционная легированная низкоуглеродистая цементируемая с сильноупрочняемой сердцевиной. Предназначена для изготовления деталей, обладающих повышенной твердостью, прочностью, износостойкостью поверхности и одновременно вязкой сердцевиной. Количество углерода: 0,09 — 0,16%.
Расшифровка: содержание углерода — 0,12%, хрома — 1,0%, никеля — 3,0%, высокого качества (А);
Химико-термообработка — слой цементации 0,6−1,2 мм, температура цементации 950−9800С, выдержка, исходя из скорости цементации, 0,1 мм/час. При массовом производстве цементацию проводим в газовых печах, при штучном или мелкосерийном производстве — в твердой среде (засыпаем углем). Если цементация проводится в газовой печи, то закалка производится непосредственно при выходе из печи, т. е. без дополнительного нагрева. После цементации все детали подвергаются упрочняющей термообработке, для ответственных деталей — двойная закалка (первая закалка — 850−870є С, вторая закалка — 760−780є С) + низкий отпуск (180−200є С), для неответственных деталей — одна закалка с цементационным нагревом (930−950є С) + низкий отпуск (180−200є С). Иногда вместо первой закалки применяют нормализацию для измельчения зерна, устранения цементитной сетки.
После полного цикла термообработки сталь имеет высокую твердость (HRC 55…64), обеспечиваемую мартенситной структурой, а сердцевина не упрочняется (35 HRC), так как в ней сохраняется ферритно-перлитная микроструктура.
Легирующие элементы по-разному влияют на превращения при химической обработке. Некоторые легирующие элементы (алюминий, кобальт) повышают мартенситную точку и уменьшают количество остаточного аустенита, другие не влияют на эту точку (кремний).
Прокаливаемость углеродистых сталей находится в прямой зависимости от содержания углерода. Для сталей с 0,8% С это примерно 5−6 мм. Легирующие элементы, увеличивая устойчивость переохлажденного аустенита, уменьшают критическую скорость Vкр закалки (исключение составляет кобальт). Поэтому некоторые легированные стали в результате охлаждения на воздухе приобретают структуру мартенсита. С уменьшением Vкр снижаются внутренние напряжения и вероятность появления брака. Однако понижение температуры мартенситного превращения способствует увеличению количества остаточного аустенита в стали после закалки.
С введением в сталь легирующих элементов закаливаемость и прокаливаемость возрастают. Особенно сильно увеличивают прокаливаемость молибден и бор (кобальт и в этом случае действует противоположно). Карбидообразующие элементы повышают прокаливаемость только в том случае, если они при нагреве растворились в аустените. В противном случае указанные элементы являются центрами распада аустенита и прокаливаемость будет даже ухудшаться. Температура нагрева легированных сталей под закалку по сравнению с углеродистыми сталями выше. Это объясняется, во-первых, тем, что большинство легирующих элементов повышает температуру критических точек Ас1 и Aс3. Во-вторых, диффузионные процессы в легированных сталях протекают значительно медленнее, так как легирующие элементы образуют твердые растворы замещения, а углерод — внедрения.
Поэтому при отпуске легирующие элементы замедляют процесс распада мартенсита: никель, марганец — незначительно; хром, молибден, кремний — заметно. Это связано с тем, что процессы при отпуске имеют диффузионный характер, а большинство элементов замедляют карбидное превращение. Легированные стали сохраняют структуру мартенсита отпуска до температуры 400−5000С. Так как в легированных сталях сохраняется значительное количество остаточного аустенита, то превращение его в мартенсит отпуска способствует сохранению твердости до высоких температур. Таким образом, легированные стали при отпуске нагревают до более высоких температур или увеличивают выдержку.
5. Укажите металлокерамические твердые сплавы для изготовления режущего инструмента. Опишите их строение, состав, свойства и способ изготовления
В настоящее время для производства режущих инструментов широко используются твердые сплавы. Они состоят из карбидов вольфрама, титана, тантала, сцементированных небольшим количеством кобальта. Карбиды вольфрама, титана и тантала обладают высокой твердостью, износостойкостью.
Инструменты, оснащенные твердым сплавом, хорошо сопротивляются истиранию сходящей стружкой и материалом заготовки и не теряют своих режущих свойств при температуре нагрева до 750−1100 °С.
Установлено что твердосплавным инструментом, имеющим в своем составе килограмм вольфрама, можно обработать 5 в раз больше материала, чем инструментом из быстрорежущей стали с тем же содержанием вольфрама.
Недостатком твердых сплавов, по сравнению с быстрорежущей сталью, является их повышенная хрупкость, которая возрастает с уменьшением содержания кобальта в сплаве. Скорости резания инструментами, оснащенными твердыми сплавами, в 3−4 раза превосходят скорости резания инструментами из быстрорежущей стали. Твердосплавные инструменты пригодны для обработки закаленных сталей и таких неметаллических материалов, как стекло, фарфор и т. п.
Производство металлокерамических твердых сплавов относится к области порошковой металлургии. Порошки карбидов смешивают с порошком кобальта. Из этой смеси прессуют изделия требуемой формы и затем подвергают спеканию при температуре, близкой к температуре плавления кобальта. Так изготовляют пластинки твердого сплава различных размеров и форм, которыми оснащаются резцы, фрезы, сверла, зенкеры, развертки и др.
Пластинки твердого сплава крепят к державке или корпусу напайкой или механически при помощи винтов и прижимов. Наряд с этим в машиностроительной промышленности применяют мелкоразмерные, монолитные твердосплавные инструменты, состоящие из твердых сплавов. Их изготовляют из пластифицированных заготовок. В качестве пластификатора в порошок твердого сплава вводят парафин до 7−9%. Из пластифицированных сплавов прессуют простые по форме заготовки, которые легко обрабатываются обычным режущим инструментом. После механической обработки заготовки спекают, а затем шлифуют и затачивают.
Из пластифицированного сплава заготовки монолитных инструментов могут быть получены путем мундштучного прессования. В этом случае спрессованные твердосплавные брикеты помещают в специальный контейнер с твердосплавным профилированным мундштуком. При продавливании через отверстие мундштука изделие принимает требуемую форму и подвергается спеканию. По такой технологии изготовляют мелкие сверла, зенкеры, развертки и т. п. Монолитный твердосплавный инструмент может также изготовляться из окончательно спеченных твердосплавных цилиндрических заготовок с последующим вышлифовыванием профиля алмазными кругами. В зависимости от химического состава металлокерамические твердые сплавы, применяемые для производства режущего инструмента, разделяются на три основные группы.
Сплавы первой группы изготовляют на основе карбидов вольфрама и кобальта. Они носят название вольфрамокобальтовых. Это сплавы группы ВК.
Ко второй группе относятся сплавы, получаемые на основе карбидов вольфрама и титана и связующего металла кобальта. Это двухкарбидные титано-вольфрамокобальтовые сплавы группы ТК. Третья группа сплавов состоит из карбидов вольфрама, титана, тантала и кобальта. Это трехкарбидные титано-танталовольфрамокобальтовые сплавы группы ТТК.
К однокарбидным сплавам группы ВК относятся сплавы: ВК3, ВК4, ВК6, ВК8, ВК10, ВК15. Эти сплавы состоят из зерен карбида вольфрама, сцементированных кобальтом. В марке сплавов цифра показывает процентное содержание кобальта. Например, сплав ВК8содержит в своем составе 92% карбида вольфрама и 8% кобальта.
Рассматриваемые сплавы применяются для обработки чугуна, цветных металлов и неметаллических материалов. При выборе марки твердого сплава учитывают содержание кобальта, которое предопределяет его прочность. Из сплавов группы ВК сплавы ВК10, ВК15, ВК8 являются наиболее вязкими и прочными, хорошо противостоят ударам и вибрациям, а сплавы ВК2, ВКЗ обладают наиболее высокой износостойкостью и твердостью при малой вязкости, слабо сопротивляются ударам и вибрациям. Сплав ВК8 применяется для черновой обработки при неравномерном сечении среза и прерывистом резании, а сплав ВК2- для чистовой отделочной обработки при непрерывном, резании с равномерным сечением среза. Для получистовых работ и черновой обработки с относительно равномерным сечением срезаемого слоя применяются сплавы ВК4, ВК6. Сплавы ВК10 и ВК15 находят применение при обработке резанием специальных труднообрабатываемых сталей.
Режущие свойства и качество твердосплавного инструмента определяются не только химическим составом сплава, но и его структурой, т. е. величиной зерна. С увеличением размера зерен карбида вольфрама прочность сплава возрастает, а износостойкость уменьшается, и наоборот.
В зависимости от размеров зерен карбидной фазы сплавы могут быть мелкозернистые, у которых не менее 50% зерен карбидных фаз имеют размер порядка 1 мкм, среднезернистые — с величиной зерна 1−2 мкм и крупнозернистые, у которых размер зерен колеблется от 2 до 5 мкм.
Для обозначения мелкозернистой структуры в конце марки сплава ставится буква М, а для крупнозернистой структуры — буква К. Буквы ОМ указывают на особо мелкозернистую структуру сплава. Буква В после цифры указывает на то, что изделия из твердого сплава спекаются в атмосфере водорода. Твердосплавные изделия одного и того же химического состава могут иметь различную структуру.
Получены особо мелкозернистые сплавы ВК6ОМ, В10ОМ, ВК150М. Сплав ВК6ОМ дает хорошие результаты при тонкой обработке жаропрочных и нержавеющих сталей, чугунов высокой твердости, алюминиевых сплавов. Сплав ВК10ОМ предназначен червовой и получерновой, а сплав ВК15ОМ — для особо тяжелых случаев обработки нержавеющих сталей, а также сплавов вольфрама, молибдена, титана и никеля.
Мелкозернистые сплавы, такие, как сплав ВК6М, используют для чистовой обработки при тонких сечениях среза стальных, чугунных, пластмассовых и других деталей. Из пластифицированных заготовок мелкозернистых сплавов ВК6М, ВК10М, ВК15М получают цельные инструменты. Крупнозернистые сплавы ВК4 В, ВК8 В, более прочные, чем обычные сплавы, применяют при резании с ударами для черновой обработки жаропрочных и нержавеющих сталей с большими сечениями среза.
При обработке сталей инструментами, оснащенными вольфрамокобальтовыми сплавами, в особенности при повышенных скоростях резания, происходит быстрое образование лунки на передней поверхности, приводящее к выкрашиванию режущей кромки сравнительно быстрому износу инструмента. Для обработки стальных заготовок применяют более износостойкие твердые сплавы группы ТК.
Сплавы группы ТК (Т30К4, Т15К6, Т14К8, Т5К10, Т5К12) состоят из зерен твердого раствора карбида вольфрама в карбиде титана и избыточных зерен карбида вольфрама, сцементированных кобальтом. В марке сплава цифра после буквы К показывает процентное содержание кобальта, а после буквы Т — процентное содержание карбидов титана. Буква В в конце марки обозначает, что сплав имеет крупнозернистую структуру.
Сплавы группы ТТК состоят из зерен твердого раствора карбида титана, карбида тантала, карбида вольфрама и избыточных зерен карбида вольфрама, сцементированных кобальтом. К сплавам группы ТТК относятся ТТ7К12, ТТ8К6, ТТ10К8Б, ТТ20К9. Сплав ТТ7К12 содержит 12% кобальта, 3% карбида тантала, 4% карбида титана и 81% карбида вольфрама.
Введение
в состав сплава карбидов тантала значительно повышает его прочность, но снижает красностойкость.
Сплав ТТ7К12 рекомендуется для тяжелых условий при обточке по корке и работе с ударами, а также для обработки специальных легированных сталей. Сплав ТТ8К6 применяют для чистовой и получистовой обработки чугуна, для непрерывной обработки с малыми сечениями среза стального литья, высокопрочных нержавеющих сталей, сплавов цветных металлов, некоторых марок титановых сплавов.
Все марки твердых сплавов разбиты по международной классификации (ИСО) на группы: К, М и Р. Сплавы группы К предназначены для обработки чугуна и цветных металлов, дающих стружку надлома. Сплавы группы М — для труднообрабатываемых материалов, сплавы группы Р — для обработки сталей.
С целью экономии дефицитного вольфрама разрабатываются безвольфрамовые металлокерамические твердые сплавы на основе карбидов, а также карбидонитридов переходных металлов, в первую очередь титана, ванадия, ниобия, тантала. Эти сплавы изготовляют на никелемолибденовой связке. Полученные твердые сплавы на основе карбидов по своим характеристикам примерно равноценны стандартным сплавам группы ТК. В настоящее время промышленностью освоены безвольфрамовые сплавы ТН-20, ТМ-3,КНТ-16 и др. Эти сплавы обладают высокой окалиностойкостью, низким коэффициентом трения, меньшим по сравнению с вольфрамсодержащими сплавами удельным весом, но имеют, как правило, более низкую прочность, склонность к разрушению при повышенных температурах. Изучение физико-механических и эксплуатационных свойств безвольфрамовых твердых сплавов показало, что они успешно могут быть использованы для чистовой и получистовой обработки конструкционных сталей и цветных сплавов, но значительно уступают сплавам группы ВК при обработке титановых и нержавеющих сталей.
Одним из путей повышения эксплуатационных характеристик твердых сплавов является нанесение на режущую часть инструмента тонких износостойких покрытий на основе нитрида титана, карбида титана, нитрида молибдена, окиси алюминия. Толщина наносимого слоя покрытия колеблется от 0,005 до 0,2 мм. Опыты показывают, что тонкие износостойкие покрытия приводят к значительному росту стойкости инструмента.
- 1. Материаловедение и технология конструкционных материалов: Учебник для вузов/ В. Б. Арзамасов, А. Н. Волчков. — М., Академия, 2009. 448 с.
- 2. Материаловедение и технология металлов: учеб. для вузов / [Фетисов Г. П. и др.]; по ред. Г. П. Фетисова. — Изд. 6-е, доп. — М.: Высш. шк., 2008. — 877 с.
- 3. Новиков И. И. Теория термической обработки металлов. — М.: Металлургия, 1986
- 4. Металловедение: Учебник для техникумов. Самохоцкий А. И., Кунявский М. Н., Кунявская Т. М.,
- 5. Парфеновская Н. Г., Быстрова Н. А. — М.: Металлургия, 1990. 416с.