Технология получения шпона на «Талион Терра»
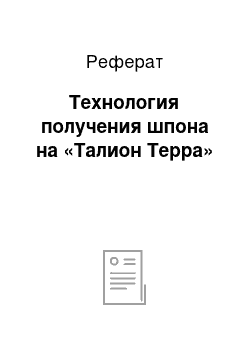
Наборка пакетов? пожалуй, наиболее интересное звено в технологии производства LVL-балок (бруса). На заводе «Талион Терра» установлена самая скоростная на сегодня станция наборки пакетов производства компании Corvallis Tool Company (США), имеющая два уровня. Скорость операции составляет 54 листа в минуту, а при необходимости может быть доведена до 81 листа. Сложность состоит в том, что наборка… Читать ещё >
Технология получения шпона на «Талион Терра» (реферат, курсовая, диплом, контрольная)
Поставщиком линии лущения была выбрана канадская компания COE Manufacturing. Кстати сказать, это, пожалуй, первый случай, когда известная финская компания RAUTE Oy проиграла канадцам тендер в России. Причем по техническим параметрам оборудования. Для работы завода на проектной мощности необходимо, чтобы лущильный станок распускал на шпон 8−10 чураков в минуту. Как показали гарантийные испытания, один канадский станок способен, «не напрягаясь», лущить до 18 чураков в минуту. Таким образом, у «Талион Терра» есть ещё и потенциал для увеличения производительности, и возможность обеспечить оптимальную производительность, используя более тонкое сырье. По требованию завода компания COE специально изготовила свое оборудование в метрической системе мер, а систему управления оснастила элементной базой Siemens. Напомним, что в Северной Америке все оборудование изготавливается в дюймовой системе мер, а для систем управления стандартно используются компоненты производства компании Allan Bradley.
Но вернемся к технологии. Из чураков получают ленту шпона толщиной 3,2 мм, её рубят на листы нужной длины, сортируют по влажности и тут же укладывают в стопы. Сортировку шпона по влажности обязательно необходимо проводить перед сушкой шпона, так как влажность заболонной и сердцевинной частей древесины после ГТО значительно разнится. Специальный механизм опорных роликов на станке СОЕ позволяет лущить чураки практически до диаметра карандаша (90 мм).
Карандаши и шпон-рванина отводятся по конвейеру и после измельчения используются как сырье для производства пеллет. Как и любое современное производство, завод «Талион Терра» задумывался и проектировался как безотходное производство, когда в дело идет вся древесина. Так называемые черные отходы? те, что образуются в процессе окорки древесины, а также отходы, которые собираются аспирационной системой завода, сжигаются в котельной. В котельной три котла суммарной тепловой мощностью 39 МВт. Один котел работает только на древесных отходах, у второго имеется дополнительная горелка для сжигания древесной пыли, а третий котел работает исключительно на природном газе. Котельную станцию для завода поставила немецкая компания Maxxtec AG.
Для сушки шпона используется 6-уровневая роликовая сушилка немецкого производства Grenzebach BSH GmbH. Сушка шпона происходит при температуре 160−200 °С пока уровень влажности материала не достигнет 5%. После сушки шпон по транспортерам поступает на линию сортировки и стопоукладки. Каждый лист шпона проходит мимо оператора линии и подвергается визуальному контролю: оператор отделяет лучшие, бессучковые листы шпона (так называемую рубашку), которые пойдут в дальнейшем на наружный слой LVL-бруса, от тех, что выглядят похуже и будут служить в качестве срединного слоя. Влажность измеряется контактным способом на устройстве для измерения влажности Elliott Bay Industries производства США. Если она выше нормы, шпон отсортировывается и отправляется на досушку.
В производстве LVL прочность шпона является очень важным фактором, поэтому на линии сортировки сухой шпон сортируют ещё и по плотности.
Сортировка происходит на оборудовании американской компании Metriguard Inc. при помощи ультразвуковых датчиков.
Благодаря такой тщательной сортировке шпон с разными физико-механическими параметрами будет затем равномерно распределен в массе готового изделия, что в результате позволит получить материал со стабильными одинаковыми характеристиками.
Высушенный, отсортированный и классифицированный шпон укладывается в стопы и погрузчиком подается в цех производства LVL-бруса.
При сушке, а также при транспортировке по конвейерам случается, что хорошие листы шпона разламываются вдоль волокон на узкие полосы. При лущении и нарезке листов из ленты шпона может быть и так, когда качество шпона высоко, но ширина листа не удовлетворяет стандартам. Для того чтобы получить форматные листы шпона из узких полосок и тем самым повысить коэффициент полезного использования древесины, существуют специальные станки. Для выполнения этой весьма тонкой операции на заводе установлены два ребросклеивающих станка производства японской фирмы Hashimoto. Полосы шпона сращиваются встык с помощью специальной термонити, которую станок укладывает на шпон и плавит. Застывая, термонить надежно скрепляет полосы друг с другом. Ребросклеивающие станки Hashimoto считаются сегодня самыми производительными в мире: каждый способен изготовить до 8 м? форматных листов шпона в час.
Подготовленный шпон подают на следующую технологическую операцию? усование: две противоположные кромки листа шпона скашивают под углом 45° на глубину 3 см.
Здесь же листы одновременно калибруются по длине и ширине, чтобы обеспечить точное совпадение скошенных кромок шпона при наборке пакета.
Листы шпона со скошенными концами подаются по транспортеру дальше.
На клееналивной машине на шпон сплошной завесой наносится изготовленный по специальной рецептуре фенолоформальдегидный клей и равномерно распределяется по одной стороне каждого листа шпона.
В производстве LVL-бруса используется клей с классом эмиссии Е 1. В качестве поставщика связующего была выбрана компания Hexion? один из крупнейших европейских производителей синтетических смол для деревообрабатывающей промышленности.
Шпон-рубашка подается по отдельному транспортеру, и клей на него наносится только в местах заусовки.
Фенолоформальдегидный клей, как и любой другой, имеет ограниченное время открытой выдержки, поэтому листы шпона с нанесенным клеем сразу подаются на станцию наборки пакетов.
Наборка пакетов? пожалуй, наиболее интересное звено в технологии производства LVL-балок (бруса). На заводе «Талион Терра» установлена самая скоростная на сегодня станция наборки пакетов производства компании Corvallis Tool Company (США), имеющая два уровня. Скорость операции составляет 54 листа в минуту, а при необходимости может быть доведена до 81 листа. Сложность состоит в том, что наборка требует высокой точности выполнения, от которой напрямую зависит качество готовой продукции. Главный технолог завода «Талион Терра» Татьяна Токарева поясняет: «Наборка пакета в производстве LVL-бруса происходит в два этапа. Набирается первый пакет, или, как мы его называем, „чешуйка“, состоящая из заданного количества листов шпона. Количество листов в „чешуйке“ определяет толщину будущего изделия. При наборке „чешуйки“ каждый лист шпона сдвигается по отношению к следующему ровно на 150 мм в сторону, противоположную движению основного конвейера линии LVL-бруса. Шпон выкладывается строго по одной линии, которая задается лазером. Когда „чешуйка“ набрана, она меняет направление движения и выкладывается на основной конвейер. Как только первая „чешуйка“ выложена на основной конвейер, уже готова следующая. Вторая „чешуйка“ выкладывается точно встык с предыдущей, накрывая её „ступеньки“. И так далее. Таким образом, получается непрерывный пакет из выкладываемых одна за другой „чешуек“ с предварительно заданным числом слоев шпона».
Отметим, Corvallis Tool Company впервые поставила свое оборудование в Россию. Оно также впервые было изготовлено в метрической системе, на базе аппаратной платформы Simotion и контроллеров Simatic ?
последних разработок компании Siemens. Проект-менеджер компании СТС Джефри Соуф делится нюансами сделки: «У нас ушел примерно год на то, чтобы спроектировать оборудование в метрической системе, перевести его на новую элементную базу и провести необходимую сертификацию. Я много времени провел в Европе, ведя переговоры с поставщиками, подбирая подходящие комплектующие. В целом стоимость оборудования из-за перехода на европейские комплектующие выросла, думаю, на 15−20%».
Сформированный таким образом непрерывный пакет из листов шпона шириной 1300 мм подается дальше по конвейеру в горячий пресс. Линию прессования поставила немецкая компания Dieffenbacher. На заводе установлен самый длинный в Европе непрырывный пресс? его длина составляет 60 м. Линия прессования LVL-бруса оснащена американской установкой предварительного нагрева пакета с помощью микроволн. Мощность установки? 500 кВт. Её задача повысить температуру внутри пакета непосредственно перед входом в горячий пресс. Предварительный нагрев позволяет увеличить скорость прессования без риска появления брака в шпоновой плите. Прессование происходит при температуре +185 °С.
После прессования непрерывная плита, двигающаяся дальше по конвейеру, проверяется на наличие непроклеенных мест и вздутий и раскраивается по длине. Систему контроля качества продукции для линии Dieffenbacher поставила компания Electronic Wood Systems GmbH. При обнаружении системой контроля качества дефектных участков диагональная пила удаляет их из шпоновой плиты. Для отвода брака предусмотрена специальная станция. Процент брака, образующегося при непрерывном прессовании, меньше, чем при прессовании на циклических прессах, и обычно не превышает 5%. А показатель разнотолщинности гораздо ниже.
Оборудование, расположенное в цепочке после пресса, предусматривает работу с заготовками максимальной длиной 20,5 м.
После обрезки по длине шпоновые плиты с помощью блока продольных пил торцуются по ширине в размер 1250 мм и раскраиваются на балки. Полученные таким образом LVL-балки, прежде чем попасть на склад готовой продукции, по конвейерам поступают на участок окончательной обработки.
Так называемая окончательная обработка очень важна, так как именно здесь производитель может задавать конкурентные преимущества своей продукции? те свойства, благодаря которым, потребитель отдаст предпочтение именно его товару, а не какому-то другому. На участке окончательной обработки завода «Талион Терра» установлено много интересного оборудования: фрезерный блок для скашивания острых кромок балки, линия маркировки и защиты кромок, линия упаковки.
Скашивание кромок, то есть создание небольшой фаски по всему периметру LVL-балки делает работу с материалом комфортной. Маркировка? обязательный атрибут, присущий высококачественному строительному материалу,? осуществляется на линии производства американской компании Claussen All-Mark Inc. Печатный оттиск наносится на пласть каждой балки и содержит логотип завода и основную информацию об изделии. Следуя по конвейеру, балки с маркировкой проходят через камеру гидрофобизации кромок. Гидрофобизацию или повышение водостойкости изделия обеспечивает распыление парафиновой эмульсии на торцы каждой LVL-балки. Это важно, так как через незащищенные торцы древесина гораздо интенсивнее впитывает влагу, чем через пласть.
Линия упаковки находится в самом конце производственной цепочки. Здесь балки согласно спецификации заказа укладываются в штабель, который перетягивается шиновальной лентой. Для того чтобы предотвратить попадание влаги при транспортировке или хранении материала на стройплощадке, его пакуют в полиэтиленовую пленку. Учитывая большую длину готового изделия, для упаковки LVL-балок используется специальная пленка, армированная текстильной сеткой. Она не порвется из-за прогиба балок и придаст штабелю дополнительную стабильность. Готовые изделия погрузчик отправляет на склад для отгрузки потребителю.